Pneumatic valve positioner for pneumatic diaphragm control valve and positioning method
A pneumatic membrane and pneumatic valve technology, applied in the direction of diaphragm valves, diaphragms, valve devices, etc., can solve the problems affecting the flow control accuracy, inaccurate valve stem positioning, etc., and achieve the effect of good flow control
- Summary
- Abstract
- Description
- Claims
- Application Information
AI Technical Summary
Problems solved by technology
Method used
Image
Examples
specific Embodiment approach 1
[0018] Specific implementation mode one: combined with figure 1 Describe this embodiment, a pneumatic valve positioner for a pneumatic film regulating valve described in this embodiment, which includes a pneumatic converter 1, a lever 2, a range spring 3, a feedback cam fulcrum 4, a feedback cam 5, a swing rod 6. Swing rod fulcrum 7, feedback lever 8, roller 9, feedback spring 10, adjustment spring 11, baffle plate 12, nozzle 13, lever fulcrum 14, air pressure amplifier 15, pneumatic film regulating valve 16, film air chamber 16-1 , valve stem 16-2.
specific Embodiment approach 2
[0019] Specific implementation mode two: combined with attached figure 1 Describe this embodiment. The difference between this embodiment and the first embodiment is that the output end of the air pressure converter 1 described in this embodiment is connected to the left side of the upper end of the lever 2, and the lever 2 The right side of the upper end is connected with one end of the range spring 3, the other end of the range spring 3 is fixed, the lever 2 is hinged on the lever fulcrum 14, and the lower end of the lever 2 is right The side is connected with one end of the feedback spring 10 and one end of the adjustment spring 11 sequentially from top to bottom, the other end of the adjustment spring 11 is fixed, and the left side of the lower end of the lever 2 is installed Described baffle plate 12, there is a certain gap between the described baffle plate 12 and the described nozzle 13, the back pressure output end of the described nozzle 13 is connected with the air p...
specific Embodiment approach 3
[0020] Specific implementation mode three: combined with attached figure 1 This embodiment is described. The difference between this embodiment and the first or second embodiment is that the air pressure converter 1 described in this embodiment is a bellows. Others are the same as those in Embodiment 1 or 2.
PUM
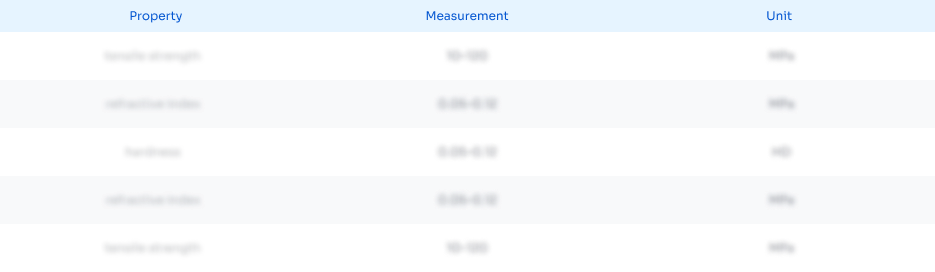
Abstract
Description
Claims
Application Information

- R&D Engineer
- R&D Manager
- IP Professional
- Industry Leading Data Capabilities
- Powerful AI technology
- Patent DNA Extraction
Browse by: Latest US Patents, China's latest patents, Technical Efficacy Thesaurus, Application Domain, Technology Topic, Popular Technical Reports.
© 2024 PatSnap. All rights reserved.Legal|Privacy policy|Modern Slavery Act Transparency Statement|Sitemap|About US| Contact US: help@patsnap.com