Repairing method of airplane composite material foam interlayer structure
A composite material and sandwich structure technology, applied in the field of repair, can solve the problems of panel bulging stiffness, unevenness, increase in weight, etc., and achieve the effects of simple operation, uniform stiffness, and flexible application.
- Summary
- Abstract
- Description
- Claims
- Application Information
AI Technical Summary
Problems solved by technology
Method used
Image
Examples
Embodiment 1
[0025] Example 1 : Repair of non-penetrating damaged composite foam interlayers.
[0026] Non-penetrating damage means that the lower panel is not damaged, only the upper panel and the foam core are removed, such as figure 2 shown. For example, the excavated area of the damaged area is a circular area with a diameter of 15 mm. Specific repairs include the following steps:
[0027] Step 1: Remove the foam and panel from the damaged part, and sand the panel;
[0028] Step 2: Cut and repair the foam, the foam is of the same model as the original structure, and the size is a cylindrical block with a diameter of 13mm, which is slightly smaller than the size of the excavated foam, which is easy to put into the damaged area;
[0029] Step 3: Grind the upper panel to form a certain bevel; the slope of the bevel is 1:20; the bevel is beneficial to the transmission of the load and to improving the flatness of the upper panel;
[0030] Step 4: Lay glue film on the upper surface of...
Embodiment 2
[0033] Example 2: Repair of penetrated composite foam sandwich structures
[0034] Penetrating damage refers to the damage that the entire sandwich (including the lower panel) is penetrated, and the upper and lower panels and the foam core need to be excavated. For example, the excavation area of the damaged area is a circular area with a diameter of 20mm, such as image 3 shown. Specific repairs include the following steps:
[0035] Step 1: Remove the foam and panel from the damaged part, and sand the panel;
[0036] Step 2: Press the panel layup form to produce the patch (the patch material is the same as the original structure), and cut and repair the foam, the diameter of the foam is 18mm;
[0037] Step 3: Glue the patch to the bottom of the lower panel. The adhesive adopts the adhesive used in the body structure. The backing plate is used to support the patch during the gluing process. Bonding quality; the patch material is the same as the original structure;
[00...
PUM
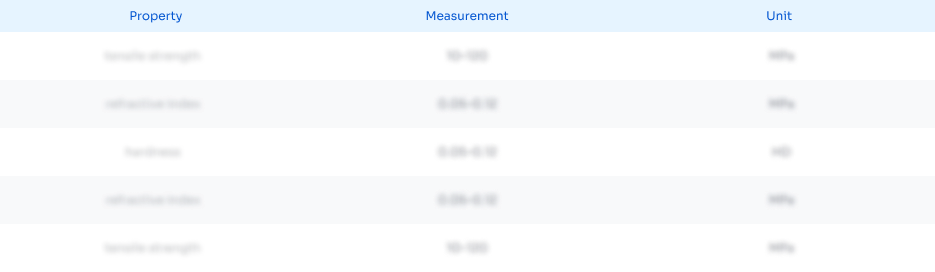
Abstract
Description
Claims
Application Information

- R&D Engineer
- R&D Manager
- IP Professional
- Industry Leading Data Capabilities
- Powerful AI technology
- Patent DNA Extraction
Browse by: Latest US Patents, China's latest patents, Technical Efficacy Thesaurus, Application Domain, Technology Topic, Popular Technical Reports.
© 2024 PatSnap. All rights reserved.Legal|Privacy policy|Modern Slavery Act Transparency Statement|Sitemap|About US| Contact US: help@patsnap.com