Double heat source hybrid welding torch and welding method
A hybrid welding and hybrid welding technology, which is applied to the welding torch of ion arc (PAW) and melting electrode arc MIG dual heat source hybrid welding. Efficiency, difficulty in stabilizing melting electrodes and non-melting electrodes, and difficulty in stabilizing double arcs in the common molten pool, to achieve the effect of improving deposition efficiency, maintaining stability, and reducing heat input
- Summary
- Abstract
- Description
- Claims
- Application Information
AI Technical Summary
Problems solved by technology
Method used
Image
Examples
Embodiment 1
[0038] figure 1 It is a structural schematic diagram of a dual heat source composite welding torch, which is a plasma arc and melting electrode MIG arc composite welding torch, which combines PAW and MIG welding in the same overall welding torch, and During the welding process, the stability of the plasma arc and the MIG arc in the communal molten pool is improved by controlling the distance D between the arc impact points on the workpiece surface, thereby improving the welding coupling efficiency of the dual heat sources. The composite welding torch includes:
[0039] ---A non-melting electrode arranged at the front end of the welding torch body 100 according to the welding direction. The non-melting electrode is a plasma electrode. Shielding sleeve 115 and compression nozzle 116; the center of compression nozzle 116 is fixed with tungsten pole 111 through tungsten pole clamp 112, cooling water channel 112 is wrapped on the outside of tungsten pole clamp 112, protective gas ...
Embodiment 2
[0050] figure 2 A structural schematic diagram of a hybrid welding system is given, which includes a composite welding torch 3 described in Example 1, a plasma power source 1, a melting electrode MIG power source 2, a wire feeding mechanism 4, a robot 5 and a controller 6, and the plasma The power supply 1 and the melting electrode MIG power supply 2 together form a double welding heat source. The composite welding torch 3 is installed on the robot 5. 3 is connected with the plasma power source 1, the melting pole MIG power source 2 and the wire feeding mechanism 4, the composite welding torch 3 is equipped with water cooling, and the water cooling tube of the composite welding torch 3 is connected with the power supply water cooling system.
PUM
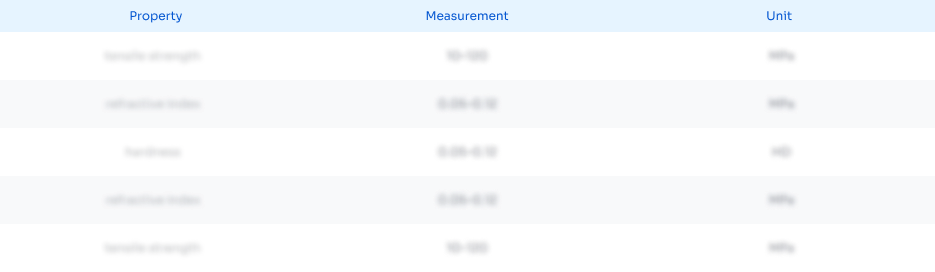
Abstract
Description
Claims
Application Information

- R&D Engineer
- R&D Manager
- IP Professional
- Industry Leading Data Capabilities
- Powerful AI technology
- Patent DNA Extraction
Browse by: Latest US Patents, China's latest patents, Technical Efficacy Thesaurus, Application Domain, Technology Topic, Popular Technical Reports.
© 2024 PatSnap. All rights reserved.Legal|Privacy policy|Modern Slavery Act Transparency Statement|Sitemap|About US| Contact US: help@patsnap.com