Method and system for restraining reduction degradation of kakoxene pellet
A technology of iron ore powder and iron ore balls, which is applied in the field of phosphate rock pellet metallurgical production, can solve serious pulverization problems such as no prevention, no suppression of reduction pulverization, and no solution to reduction pulverization, so as to solve the problem of phosphate rock reduction Effects of pulverization, porosity reduction, and energy consumption reduction
- Summary
- Abstract
- Description
- Claims
- Application Information
AI Technical Summary
Problems solved by technology
Method used
Image
Examples
Embodiment 1
[0041] (1) Grinding the phosphate iron ore to obtain phosphate iron ore powder, requiring that the ratio of the particle size of the phosphate iron ore powder to be less than 0.074mm is between 60% and 80%;
[0042] (2) mix ferrophosphite powder and bentonite evenly to obtain a mixture; the specific proportioning ratio is 95 kg of ferric phosphorite powder and 5 kg of bentonite;
[0043] (3) The mixture is pelletized on a pelletizing machine (disc pelletizing machine) to make green pellets, and the pellets are balls with a diameter of 10-18mm; wherein boric acid aqueous solution is added as pelletizing pellets during the pelletizing process. Ball water; the concentration of the boric acid aqueous solution is 0.2% (mass percentage), and the total mass of the phosphorite powder and bentonite is 100%, and the addition of the boric acid aqueous solution is 1%. The addition point of the boric acid aqueous solution is the water addition point of the pelletizing machine. Firstly, bor...
Embodiment 2
[0047] (1) Grinding the phosphate iron ore to obtain phosphate iron ore powder, requiring that the ratio of the particle size of the phosphate iron ore powder to be less than 0.074mm is between 60% and 80%;
[0048] (2) mix ferriphosphite powder and bentonite evenly to obtain a mixture; the specific proportioning is 99 kg of ferriphosphite powder and 1 kg of bentonite;
[0049] (3) The mixture is pelletized on a pelletizing machine (cylindrical pelletizing machine) to make green pellets, and the pellets are round balls with a diameter of 10-18mm; wherein boric acid aqueous solution is added as pelletizing pellets during the pelletizing process. Ball water; the concentration of the boric acid aqueous solution is 0.5% (mass percentage), and the total mass of the phosphorite powder and bentonite is 100%, and the addition of the boric acid aqueous solution is 2%. The addition point of the boric acid aqueous solution is the water addition point of the pelletizing machine. Firstly, ...
Embodiment 3
[0053] (1) Grinding the phosphate iron ore to obtain phosphate iron ore powder, requiring that the ratio of the particle size of the phosphate iron ore powder to be less than 0.074mm is between 60% and 80%;
[0054] (2) mix ferriphosphite powder and bentonite evenly to obtain a mixture; the specific proportioning is 97kg of ferriphosphite powder and 3kg of bentonite;
[0055] (3) The mixture is pelletized on a pelletizing machine (disc pelletizing machine) to make green pellets, and the pellets are balls with a diameter of 10-18mm; wherein boric acid aqueous solution is added as pelletizing pellets during the pelletizing process. Ball water; the concentration of the boric acid aqueous solution is 0.8% (mass percentage), and the total mass of the phosphorite powder and bentonite is 100%, and the addition of the boric acid aqueous solution is 1.5%. The addition point of the boric acid aqueous solution is the water addition point of the pelletizing machine. Firstly, boric acid an...
PUM
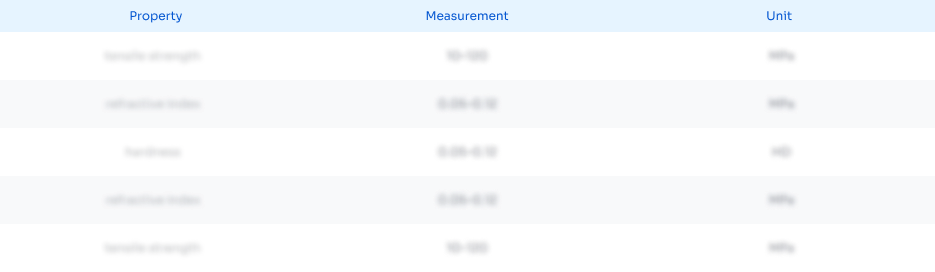
Abstract
Description
Claims
Application Information

- R&D
- Intellectual Property
- Life Sciences
- Materials
- Tech Scout
- Unparalleled Data Quality
- Higher Quality Content
- 60% Fewer Hallucinations
Browse by: Latest US Patents, China's latest patents, Technical Efficacy Thesaurus, Application Domain, Technology Topic, Popular Technical Reports.
© 2025 PatSnap. All rights reserved.Legal|Privacy policy|Modern Slavery Act Transparency Statement|Sitemap|About US| Contact US: help@patsnap.com