Low-temperature preparation method of ceramic coating absorbing waves in frequency band of 8-18 GHz
A ceramic coating and low-temperature technology, which is applied in coatings, radiation-absorbing coatings, metal material coating processes, etc., can solve the problems of unsuitable temperature and low temperature resistance, and achieve optimized microwave absorption performance and improved microwave absorption performance, wide range of applications
- Summary
- Abstract
- Description
- Claims
- Application Information
AI Technical Summary
Problems solved by technology
Method used
Image
Examples
preparation example Construction
[0031] Aiming at the preparation process of the wave absorbing coating, the present invention proposes a low-temperature preparation method of the coating that combines the "painting technology" with the "chemical vapor deposition technology". figure 1 shown. The preparation process mainly includes the following three core links:
[0032] (1) batching, mix the wave absorbing agent with the materials such as binder, plasticizer and solvent evenly;
[0033] (2) painting, evenly painting the mixed slurry in (1) on the surface of the base material;
[0034] (3) Deposition, in (2) the chemical vapor deposition of the wave-transmitting coating on the surface of the material.
[0035] Specifically, firstly, ingredients are the basic link of the present invention. In order to evenly coat the wave absorber on the surface of the composite material, it is necessary to add a variety of organic substances to form a slurry with a certain viscosity. The organic components added include: ...
Embodiment 1
[0041] The two-dimensional SiC fiber toughened SiBCN matrix composite material was selected as the base material, and the material size was 180mm×180mm×3.2mm. The mixed powder formed by 40wt.% A powder and 60wt.% B powder is selected as the wave absorbing agent (wherein, the A powder is the SiBCN powder containing nano-SiC that has undergone high temperature heat treatment, and the B powder is the nanometer-free powder that has not been heat treated at high temperature. SiC SiBCN powder). The volume fraction of mixed powder in the slurry is 30%, the volume fraction of solvent is 60%, the volume fraction of dispersant and binder is 3%, and the volume fraction of plasticizer and defoamer is 2%. Brushing was started immediately after the slurry was sonicated for 2 hours. After painting, the composites were allowed to stand for 12 hours in room temperature air. After the slurry was dried in the shade, the composite material was placed in a vacuum reactor for chemical vapor depos...
Embodiment 2
[0043] select Al 2 O 3 The fiber mat reinforced SiCN matrix composite material was used as the base material, and the material size was 180mm×180mm×2mm. Multi-walled carbon nanotubes (MWCNTs) were selected as the absorber. The volume fraction of wave absorber in the slurry is 15%, the volume fraction of solvent is 75%, the volume fraction of dispersant and binder is 3%, and the volume fraction of plasticizer and defoamer is 2%. Brushing was started immediately after the slurry was sonicated for 1 hour. After painting, the composites were allowed to stand for 12 hours in room temperature air. After the slurry was dried in the shade, the composite material was placed in a vacuum reactor for chemical vapor deposition B 4 C. The reaction temperature is 950℃, and the precursor system is BCl 3 -CH 4 -H 2 -Ar, [B]:[C]=3:1. After the preparation of the absorbing coating was completed, the electromagnetic properties of the composite materials were tested in the range of 8-18 G...
PUM
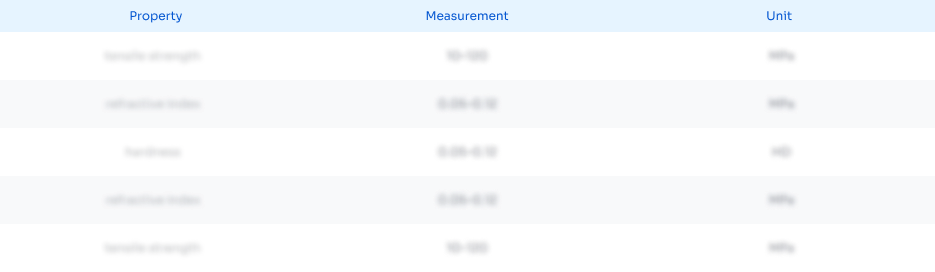
Abstract
Description
Claims
Application Information

- Generate Ideas
- Intellectual Property
- Life Sciences
- Materials
- Tech Scout
- Unparalleled Data Quality
- Higher Quality Content
- 60% Fewer Hallucinations
Browse by: Latest US Patents, China's latest patents, Technical Efficacy Thesaurus, Application Domain, Technology Topic, Popular Technical Reports.
© 2025 PatSnap. All rights reserved.Legal|Privacy policy|Modern Slavery Act Transparency Statement|Sitemap|About US| Contact US: help@patsnap.com