Alloy type catalyst for lightening heavy aromatics and preparation method thereof
A technology for lightening heavy aromatics and catalysts, which is applied in the field of alloy-type heavy aromatics lightening catalysts and its preparation, which can solve the problems of fast catalyst deactivation rate, low yield of single-ring aromatics, and low conversion depth of heavy aromatics. Achieve the effects of slow deactivation rate, high yield and high conversion depth
- Summary
- Abstract
- Description
- Claims
- Application Information
AI Technical Summary
Problems solved by technology
Method used
Image
Examples
Embodiment 1
[0037] Add 60g of HY molecular sieve (commercially available) with a silicon-aluminum ratio of 10 and 30g of pseudo-boehmite (commercially available) on a dry basis into the mixer until uniform, then add 3g of turnip powder and 5g of HNO at a volume ratio of 1:1 to the mixture. 3 solution and 40g deionized water, and grind evenly to make a dough suitable for extrusion. It is extruded through a die and is in the shape of a slender cylinder (diameter 1.7mm). After drying at 120°C, it is baked at 550°C for 4 hours, and then it is cut into carrier particles (1.7×4.0mm) of uniform size for use.
[0038] The mixed solution of chloroiridic acid, nickel nitrate, and zinc nitrate was used to impregnate the carrier particles at 40°C, and the dry basis weight of the carrier contained in the impregnation solution was 0.2% Ir, 4% Ni and 1% Zn, aged for 8h and passed After drying, it was oxidized in air at 900°C for 4 hours, and then reduced in hydrogen at 700°C for 4 hours (this step can b...
Embodiment 2
[0041] Add 60g of Beta molecular sieve (commercially available) with a silicon-aluminum ratio of 15 and 30g of pseudoboehmite (commercially available) on a dry basis into the mixer until uniform, then add 3g of scallop powder and 5g of HNO with a volume ratio of 1:1 to the mixture. 3 solution and 40g deionized water, and grind evenly to make a dough suitable for extrusion. It is extruded through a die and is in the shape of a slender cylinder (diameter 1.7mm). After drying at 120°C, it is baked at 550°C for 4 hours, and then it is cut into carrier particles (1.7×4.0mm) of uniform size for use.
[0042] The mixed solution of chloroiridic acid, nickel nitrate, and zinc nitrate was used to impregnate the carrier particles at 40°C, and the dry basis weight of the carrier contained in the impregnation solution was 0.2% Ir, 4% Ni and 1% Zn, aged for 8h and passed After drying, oxidize in air at 900°C for 4 hours, and then reduce in hydrogen at 700°C for 4 hours (this step can be com...
Embodiment 3
[0045] Add 60g of MOR molecular sieve (commercially available) with a silicon-aluminum ratio of 30 and 30g of pseudoboehmite (commercially available) on a dry basis into the mixer until uniform, then add 3g of turnip powder, 5g of HNO at a volume ratio of 1:1 to the mixture 3 solution and 40g deionized water, and grind evenly to make a dough suitable for extrusion. It is extruded through a die and is in the shape of a slender cylinder (diameter 1.7mm). After drying at 120°C, it is baked at 550°C for 4 hours, and then it is cut into carrier particles (1.7×4.0mm) of uniform size for use.
[0046] The mixed solution of chloroiridic acid, nickel nitrate, and zinc nitrate was used to impregnate the carrier particles at 40°C, and the dry basis weight of the carrier contained in the impregnation solution was 0.2% Ir, 4% Ni and 1% Zn, aged for 8h and passed After drying, oxidize in air at 900°C for 4h, and then reduce in hydrogen at 700°C for 4h (this step can be completed in a reacto...
PUM
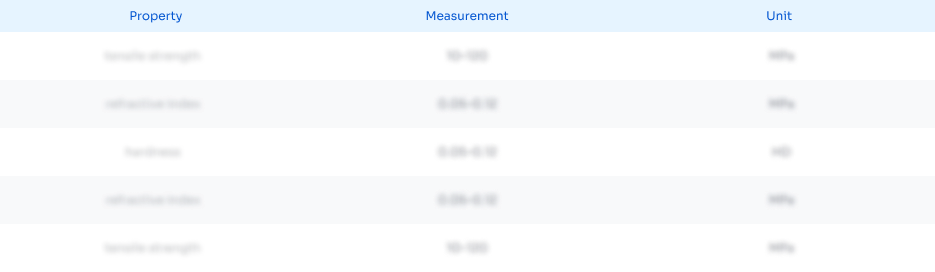
Abstract
Description
Claims
Application Information

- R&D
- Intellectual Property
- Life Sciences
- Materials
- Tech Scout
- Unparalleled Data Quality
- Higher Quality Content
- 60% Fewer Hallucinations
Browse by: Latest US Patents, China's latest patents, Technical Efficacy Thesaurus, Application Domain, Technology Topic, Popular Technical Reports.
© 2025 PatSnap. All rights reserved.Legal|Privacy policy|Modern Slavery Act Transparency Statement|Sitemap|About US| Contact US: help@patsnap.com