High-performance environment-friendly building-use ceramic material and preparation method thereof
A technology for ceramic materials and construction, applied in the field of high-performance and environmentally friendly construction ceramic materials and their preparation, can solve the problems of affecting the economic benefits of enterprises, lack of scientific and strict management, and high production costs, and achieve good compactness, high strength, The effect of excellent comprehensive performance
- Summary
- Abstract
- Description
- Claims
- Application Information
AI Technical Summary
Problems solved by technology
Method used
Examples
preparation example Construction
[0020] A method for preparing a high-performance and environment-friendly building ceramic material, comprising the steps of:
[0021] S1. Weigh a certain amount of 20-35 parts of heated converter slag, 20-30 parts of borax decahydrate, 15-30 parts of albite, 10-20 parts of shale, 8-15 parts of crop straw, and 20 parts of epoxy resin. -35 parts and 8-12 parts of coke gemstones were respectively added to a pulverizer for pulverization and then mixed, and passed through a 90-110 mesh filter sieve to obtain a mixed powder;
[0022] S2. Pour the powder obtained in step S1 into a mixer and add water, then add 9-15 parts of dibutyl phthalate, 3-7 parts of titanate coupling agent, 10-16 parts of paraffin oil, and 5- 10 parts, 10-12 parts of glaze paddle, 5-10 parts of sintering aid, stir quickly and evenly, and then perform ball milling for 15-30min to obtain ceramic slurry;
[0023] S3. The ceramic slurry obtained in step S2 is molded by a ceramic brick press, and fired in a kiln a...
Embodiment 1
[0026] S1. Weigh a certain amount of 28 parts of hot-steamed converter slag, 26 parts of borax decahydrate, 18 parts of albite, 17 parts of shale, 11 parts of crop straw, 26 parts of epoxy resin, and 11 parts of burnt gemstones, and add them to the pulverizer respectively Mix after pulverizing, and pass through a 99-mesh filter sieve to obtain a mixed powder;
[0027] S2. Pour the powder obtained in step S1 into a blender, add water, add 13 parts of dibutyl phthalate, 6 parts of titanate coupling agent, 15 parts of paraffin oil, 8 parts of ceramic pigment, 11 parts of glaze paddle, 7 parts of sintering aids were quickly stirred evenly, and then ball milled for 22 minutes to obtain ceramic slurry;
[0028] S3. The ceramic slurry obtained in step S2 is molded by a ceramic brick press, and fired in a kiln at a firing temperature of 1100° C. to obtain a primary ceramic product;
[0029] S4. After the primary ceramic product obtained in step S3 is ground and roasted, it is inspect...
Embodiment 2
[0031] S1. Weigh a certain amount of 35 parts of hot-simmered converter slag, 30 parts of borax decahydrate, 30 parts of albite, 20 parts of shale, 15 parts of crop straw, 35 parts of epoxy resin, and 12 parts of burnt gemstones, and add them to the pulverizer respectively Mix after pulverizing, and pass through a 110-mesh filter sieve to obtain a mixed powder;
[0032] S2. Pour the powder obtained in step S1 into a mixer and add water, followed by adding 15 parts of dibutyl phthalate, 7 parts of titanate coupling agent, 16 parts of paraffin oil, 10 parts of ceramic pigment, 12 parts of glaze paddle, 10 parts of sintering aids were mixed quickly and evenly, and then ball milled for 30 minutes to obtain ceramic slurry;
[0033] S3. The ceramic slurry obtained in step S2 is molded by a ceramic brick press, and fired in a kiln at a firing temperature of 1000-1200° C. to obtain a primary ceramic product;
[0034] S4. After the primary ceramic product obtained in step S3 is ground...
PUM
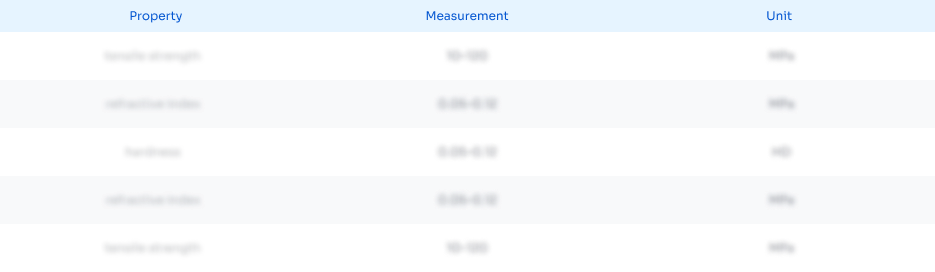
Abstract
Description
Claims
Application Information

- R&D
- Intellectual Property
- Life Sciences
- Materials
- Tech Scout
- Unparalleled Data Quality
- Higher Quality Content
- 60% Fewer Hallucinations
Browse by: Latest US Patents, China's latest patents, Technical Efficacy Thesaurus, Application Domain, Technology Topic, Popular Technical Reports.
© 2025 PatSnap. All rights reserved.Legal|Privacy policy|Modern Slavery Act Transparency Statement|Sitemap|About US| Contact US: help@patsnap.com