Slurry and preparation method thereof
A slurry and fabric technology, applied in the field of slurry and preparation, can solve the problems of ink color fastness not meeting the requirements and the color is not bright, and achieve the effect of improving the color fastness and maintaining the vividness.
- Summary
- Abstract
- Description
- Claims
- Application Information
AI Technical Summary
Problems solved by technology
Method used
Image
Examples
Embodiment Construction
[0020] A slurry of this embodiment is used for sizing cloth before inkjet printing, and the slurry is composed of the following components in parts by weight: 63 parts of water, 4-10 parts of urea, 1.3-2 parts of baking soda 0.75 parts of sodium alginate, 1.8 parts of starch, and 0.5-1 part of anti-staining salt. Urea can fully expand the fiber during the color fixing process, create conditions for the reaction of reactive dyes and fibers, and facilitate the ink to fully penetrate into the fabric. Baking soda will affect the coloring rate of the ink in the process of steaming and fixing the color, and play a role in fixing the color. Sodium alginate is a thickener, which can prevent the ink sprayed on the cloth from bleeding during the subsequent steaming and color fixing process, which will affect the fineness of the pattern. Starch is the paste. Sodium alginate cooperates with starch to facilitate ink penetration and improve color fastness. As a weak oxidizing agent, anti...
PUM
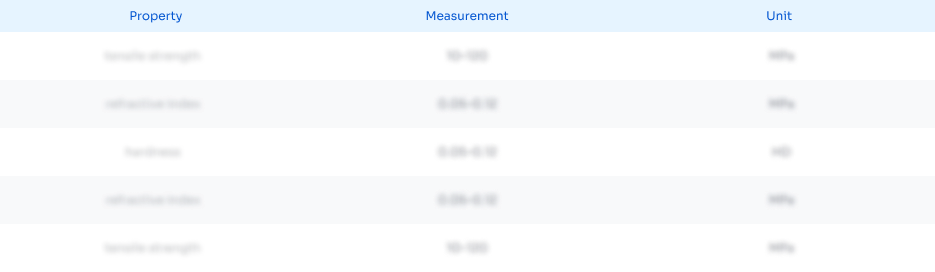
Abstract
Description
Claims
Application Information

- Generate Ideas
- Intellectual Property
- Life Sciences
- Materials
- Tech Scout
- Unparalleled Data Quality
- Higher Quality Content
- 60% Fewer Hallucinations
Browse by: Latest US Patents, China's latest patents, Technical Efficacy Thesaurus, Application Domain, Technology Topic, Popular Technical Reports.
© 2025 PatSnap. All rights reserved.Legal|Privacy policy|Modern Slavery Act Transparency Statement|Sitemap|About US| Contact US: help@patsnap.com