Method for removing volatile substances in polyether polyol and reducing smell
A technology for polyether polyols and volatile substances, applied in the field of polyether polyols, can solve the problems of improving the removal effect of small molecular impurities, and achieve the effects of reducing odor, satisfying health, and reducing volatile components
- Summary
- Abstract
- Description
- Claims
- Application Information
AI Technical Summary
Problems solved by technology
Method used
Image
Examples
Embodiment 1
[0044] Add 40g of glycerin into the reaction kettle as a starter, KOH accounting for 0.5wt% of the total mass as a catalyst, after nitrogen replacement and dehydration, successively add 2100g of propylene oxide and 370g of epoxy at 100°C and no more than 0.5MPa. Ethane, after feeding and aging, a polyether polyol (referred to as polyether) with a functionality of 3 and a molecular weight of 5000 was obtained. Take 2000g of the above-mentioned polyether, add 0.3wt% phosphoric acid aqueous solution through the distributor at the bottom of the tank for neutralization, then add 0.5wt% magnesium silicate and 2wt% diatomaceous earth, heat up and vacuum dehydrate, while nitrogen bubbles, and finally add Press filter 2 times. Add 0.3% by mass fraction of pentaerythritol bisphosphite and 5ppm of sodium borohydride to the obtained refined polyether polyol. The polyether then enters the stripping tower, and the triangular cone packing is filled into the tower at intervals. The temperat...
Embodiment 2
[0046] Referring to the steps and conditions in Example 1, add 51g of sorbitol to the reactor as a starter, and KOH accounting for 0.5wt% of the total mass as a catalyst. Continuously add 2200g of propylene oxide and 245g of ethylene oxide in sequence, after feeding and aging, a polyether with a functionality of 6 and a molecular weight of 8000 is obtained. Take 2000g of the above polyether, add 0.5wt% oxalic acid for neutralization, then add 1wt% magnesium silicate and 1wt% diatomaceous earth for refining. Add 0.1% of pentaerythritol bisphosphite and 4ppm of sodium borohydride to the refined polyether. The operating temperature of the stripping tower is 130°C, the pressure is -0.07MPa, and the flow volume ratio of water vapor to polyether is 2. The operating temperature of the short path evaporator is 150°C and the vacuum degree is 0.3mbar. All the above contents are based on the mass of polyether, the same below.
Embodiment 3
[0048] With reference to the steps and conditions in Example 1, add 83g of propylene glycol as a starter to the reactor, and KOH accounting for 0.5wt% of the total mass as a catalyst. After nitrogen replacement and dehydration, continue at 100°C and no more than 0.5MPa 2400g of propylene oxide was added, and after feeding and aging, a polyether with a functionality of 2 and a molecular weight of 2000 was obtained. Take 2000 g of the above-mentioned polyether, add 0.8wt% acetic acid, 2wt% aluminum silicate and 0.5wt% acid clay for refining in sequence. Subsequently, 1% by mass fraction of 2,8-di-tert-butyl-4-methylphenol and 1 ppm of sodium thiosulfate were added to the polyether. The operating temperature of the stripper is 160°C, the pressure is -0.09MPa, and the flow volume ratio of water vapor to polyether is 0.5. The operating temperature of the short path evaporator is 160°C and the vacuum degree is 10mbar. All the above contents are based on the mass of polyether, the ...
PUM
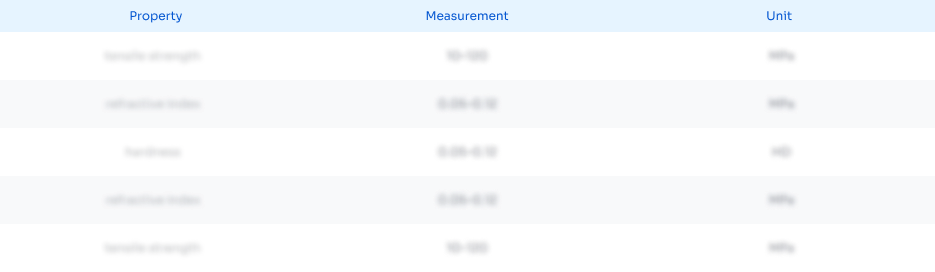
Abstract
Description
Claims
Application Information

- R&D Engineer
- R&D Manager
- IP Professional
- Industry Leading Data Capabilities
- Powerful AI technology
- Patent DNA Extraction
Browse by: Latest US Patents, China's latest patents, Technical Efficacy Thesaurus, Application Domain, Technology Topic, Popular Technical Reports.
© 2024 PatSnap. All rights reserved.Legal|Privacy policy|Modern Slavery Act Transparency Statement|Sitemap|About US| Contact US: help@patsnap.com