Heat treatment method for high-temperature alloy steel
A technology of superalloy steel and heat treatment method, which is applied in the field of heat treatment of superalloy steel, and can solve the problems of no reference value, no process parameters such as alloy solution treatment and aging treatment suitable temperature, etc., and it is difficult to achieve superalloy heat treatment process. , to achieve the effect of good high temperature plasticity and creep resistance life
- Summary
- Abstract
- Description
- Claims
- Application Information
AI Technical Summary
Problems solved by technology
Method used
Examples
Embodiment 1
[0035] A sort of The high-temperature diffusion annealing process for GH4169 high-temperature alloy steel ingots of different sizes is as follows: 1150±10°C, heat preservation for 24 hours, and then air-cooling at 1190±10°C for 72 hours, and after 7 times of pier thickening and elongation thermal processing, the pier thickness reaches For round cakes, the subsequent heat treatment process includes the following steps:
[0036] (1) Pretreatment after forging: heating temperature is 960°C, heat preservation for 1h, and air cooling;
[0037] (2) High temperature solution treatment: heating temperature is 900°C, heat preservation for 22h, air cooling; reheating, heating temperature is 950°C, heat preservation for 1.5h, air cooling;
[0038] (3) Low-temperature aging treatment: heating temperature is 720°C, heat preservation for 8 hours, cooling to 620°C with the furnace at a rate of 50°C / h, heat preservation for 8 hours, and air cooling.
[0039] The final grain level of the f...
Embodiment 2
[0042] A sort of The high-temperature diffusion annealing process for GH4169 high-temperature alloy steel ingots of different sizes is as follows: heat preservation at 1150±10°C for 24 hours, then heat preservation at 1190±10°C for 72 hours, and air cooling. For round cakes, the subsequent heat treatment process includes the following steps:
[0043] (1) Pretreatment after forging: heating temperature is 950°C, heat preservation for 1h, and air cooling;
[0044](2) High temperature solution treatment: heating temperature is 910°C, heat preservation for 24 hours, air cooling, reheating, heating temperature is 960°C, heat preservation for 2 hours, air cooling;
[0045] (3) Low-temperature aging treatment: heating temperature is 710°C, heat preservation for 9 hours, cooling with the furnace at a rate of 60°C / h to 610°C, heat preservation for 9 hours, and air cooling.
[0046] The final grain level of the forging is 8.2;
[0047] The forgings were subjected to high temperatur...
Embodiment 3
[0049] A sort of The high-temperature diffusion annealing process for GH4169 high-temperature alloy steel ingots of different sizes is as follows: heat preservation at 1150±10°C for 24 hours, then heat preservation at 1190±10°C for 72 hours, and air cooling. For round cakes, the subsequent heat treatment process includes the following steps:
[0050] (1) Pretreatment after forging: heating temperature is 940°C, heat preservation for 1h, and air cooling;
[0051] (2) High temperature solution treatment: heating temperature is 920°C, heat preservation 18h, air cooling, reheating, heating temperature is 970°C, heat preservation 1h, air cooling;
[0052] (3) Low-temperature aging treatment: Heating temperature is 700°C, heat preservation for 10h, cooling with the furnace at a speed of 55°C / h to 600°C, heat preservation for 7h, and air cooling.
[0053] The final grain grade of the forging is 8.4;
[0054] The forgings were subjected to high-temperature and low-cycle creep-fat...
PUM
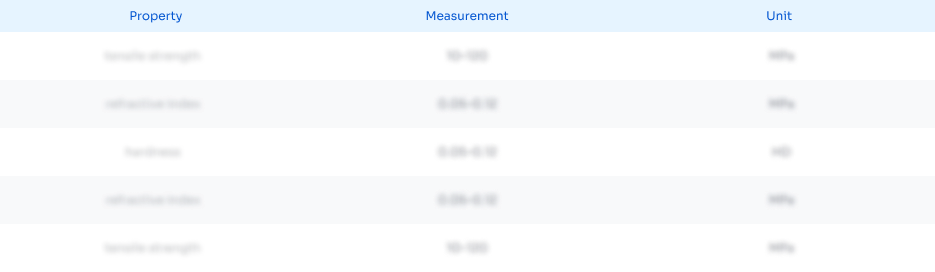
Abstract
Description
Claims
Application Information

- R&D Engineer
- R&D Manager
- IP Professional
- Industry Leading Data Capabilities
- Powerful AI technology
- Patent DNA Extraction
Browse by: Latest US Patents, China's latest patents, Technical Efficacy Thesaurus, Application Domain, Technology Topic, Popular Technical Reports.
© 2024 PatSnap. All rights reserved.Legal|Privacy policy|Modern Slavery Act Transparency Statement|Sitemap|About US| Contact US: help@patsnap.com