Processing method of integral guide apparatus
A processing method and technology of guides, which are applied in the direction of machines/engines, stators, engine components, etc., can solve problems such as cracking of brazing seams, and achieve the effects of precise dimensions, reduced manufacturing costs, and improved processing efficiency
- Summary
- Abstract
- Description
- Claims
- Application Information
AI Technical Summary
Problems solved by technology
Method used
Image
Examples
Embodiment 1
[0028] (1) Part status
[0029] The integral guide is composed of front mounting edge 1, rear mounting edge 5, blade assembly (18 pieces) 6, bellows 3 and bellows front ring 2. The structure of the integral guide is as follows: figure 1 shown. The material of the front mounting edge 1, the rear mounting edge 5 and the bellows front ring 2 is GH3044 superalloy, the material of the bellows 3 is GH3030 superalloy, and the material of the blade assembly (18 pieces) 6 is K403 superalloy.
[0030] (2) Processing equipment
[0031] The main processing equipment includes: vacuum electron beam welding machine, energy storage spot welding machine, vacuum brazing furnace and large lathe.
[0032] (3) Implementation process
[0033] Step 1: Processing preparation
[0034] Pre-assemble the front mounting edge 1, blade (18 pieces) 6, and rear mounting edge 5 on the assembly fixture, and control the amount of misalignment between the blade edge plate assembly edges by selecting blades to...
Embodiment 2
[0052] (1) Part status
[0053] The integral guide is composed of front mounting edge 1, rear mounting edge 5, blade assembly 618 pieces), bellows 3 bellows front ring 2, and the structure of the integral guide is as follows figure 1 shown. The material of the front mounting 1, the rear mounting edge 5 and the bellows front ring 2 is GH4648 superalloy, the material of the bellows 3 is GH3030 superalloy, and the material of the blade assembly (18 pieces) is K403 superalloy.
[0054] (2) Processing equipment
[0055] The main processing equipment includes: vacuum electron beam welding machine, energy storage spot welding machine, vacuum brazing furnace, large lathe.
[0056] (3) Implementation process
[0057] Step 1: Processing preparation
[0058] Pre-assemble the front mounting edge 1, blade 6a (18 pieces), and rear mounting edge 5 on the assembly fixture, and control the amount of misalignment between the blade edge plate assembly edges by selecting blades to be no more ...
PUM
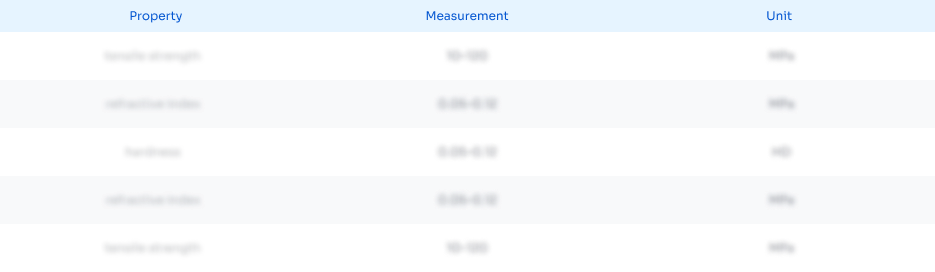
Abstract
Description
Claims
Application Information

- R&D
- Intellectual Property
- Life Sciences
- Materials
- Tech Scout
- Unparalleled Data Quality
- Higher Quality Content
- 60% Fewer Hallucinations
Browse by: Latest US Patents, China's latest patents, Technical Efficacy Thesaurus, Application Domain, Technology Topic, Popular Technical Reports.
© 2025 PatSnap. All rights reserved.Legal|Privacy policy|Modern Slavery Act Transparency Statement|Sitemap|About US| Contact US: help@patsnap.com