Laser additive manufacturing method applied to large-sized metal part
A technology for laser additive manufacturing and metal parts, which is used in additive manufacturing, additive processing, and process efficiency improvement. It can solve the heat accumulation effect of parts, the difficulty in controlling the quality of laser additive manufacturing of large metal parts, and complex thermal stress. problems, to avoid deformation and cracking, improve the quality of laser additive manufacturing, and reduce the effect of heat accumulation
- Summary
- Abstract
- Description
- Claims
- Application Information
AI Technical Summary
Problems solved by technology
Method used
Image
Examples
Embodiment Construction
[0032] The present invention will be further described in detail below in conjunction with the accompanying drawings and specific embodiments.
[0033] A laser additive manufacturing method suitable for large metal parts, comprising the steps of:
[0034] Step 1: Block parts
[0035] According to the configuration characteristics and load distribution characteristics of the overall structure of the part, the part is divided into several sub-blocks; by dividing the part into blocks, the heat accumulation effect in the subsequent laser additive manufacturing process can be effectively reduced, thereby reducing the internal stress, effectively Avoid deformation and cracking;
[0036] Step 2: Subblock Partitioning
[0037] According to the shape and structure characteristics of each sub-block, several scanning areas are divided in each sub-block; when several scanning areas in the sub-block are divided, the scanning order needs to be sorted, and sorted according to the principle...
PUM
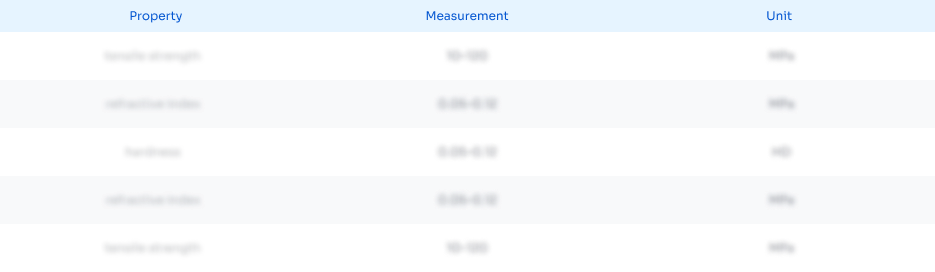
Abstract
Description
Claims
Application Information

- Generate Ideas
- Intellectual Property
- Life Sciences
- Materials
- Tech Scout
- Unparalleled Data Quality
- Higher Quality Content
- 60% Fewer Hallucinations
Browse by: Latest US Patents, China's latest patents, Technical Efficacy Thesaurus, Application Domain, Technology Topic, Popular Technical Reports.
© 2025 PatSnap. All rights reserved.Legal|Privacy policy|Modern Slavery Act Transparency Statement|Sitemap|About US| Contact US: help@patsnap.com