Stress test method in rotation state
A stress test and stress technology, applied in the direction of measuring force, measuring devices, instruments, etc., can solve the problems of easy entanglement of wiring, lack of data acquisition, and inability to carry out experiments, etc., and achieve the effect of light weight and small volume
- Summary
- Abstract
- Description
- Claims
- Application Information
AI Technical Summary
Problems solved by technology
Method used
Image
Examples
Embodiment 1
[0033] Such as Figure 1-2 As shown, this embodiment provides a stress test method for rotation, taking an inverted umbrella aerator as an example, the test process is as follows:
[0034] 1) First obtain the rotation speed of the inverted umbrella of the inverted umbrella aerator, and determine that its rotation speed is low-speed rotation,
[0035] 2) Since its rotation speed is low-speed rotation, a data transmission device with a slightly larger volume is selected to facilitate the real-time transmission of the stress state of the inverted umbrella.
[0036] 3) Stand the stress sheet on the inverted umbrella sheet 1 of the aerator, and let the stress sheet rotate with the inverted umbrella. The data transmission equipment and the power supply are installed on the inverted umbrella base 2, so that the power supply and the data transmission equipment rotate together with the inverted umbrella while minimizing the rotation range.
[0037] 4) The wires of the stress gauge ar...
Embodiment 2
[0045] On the basis of the above-mentioned embodiments, the steps of installing the stress plate, power supply and data processing device are as follows:
[0046] Paste the stress sheet on the position to be measured of the workpiece to be measured,
[0047] Fix the power supply and data processing device in the non-working area of the workpiece to be tested,
[0048] Arrange the power line and data line on the workpiece to be tested, and electrically connect the power supply, data processing device and stress gauge through the power line and data line.
[0049] After the data transmission device and / or the data storage device are installed, a protective shell is installed outside the data transmission device and / or the data storage device, and the protective shell is fixedly connected to the workpiece to be measured .
[0050] Since the stress sheet needs to measure the stress change in the working process of the workpiece, it is necessary to paste the stress sheet on the...
Embodiment 3
[0053] On the basis of the above-mentioned embodiments, the adjustment of the relational model is also included:
[0054] Execute steps 1)-5) to obtain several sets of data,
[0055] Compare the data with the relational model respectively. If the error between the relational model and the data is not greater than the error threshold, maintain the existing model state. If the error between the relational model and the data is greater than the error threshold, perform the following steps:
[0056] In step 4) evenly select some rotation speed values between every adjacent two rotation speed values,
[0057] In step 5) evenly select some inclination angle values between every adjacent two inclination angles,
[0058] Execute the selected rotation speed value and tilt angle value in steps 1)-5),
[0059] According to the data obtained in steps 1)-5), the relationship model between the rotation speed and the stress at each angle is corrected.
[0060]Due to the problem of dat...
PUM
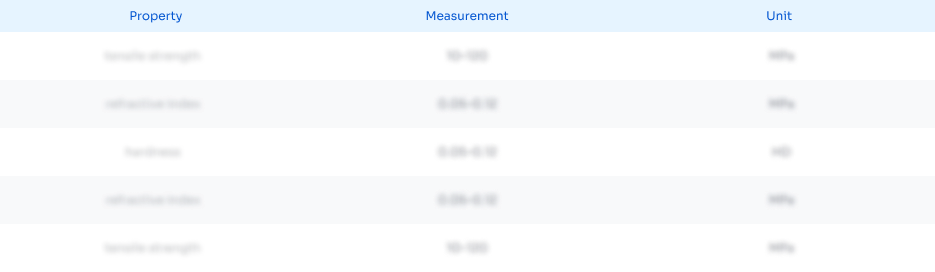
Abstract
Description
Claims
Application Information

- R&D
- Intellectual Property
- Life Sciences
- Materials
- Tech Scout
- Unparalleled Data Quality
- Higher Quality Content
- 60% Fewer Hallucinations
Browse by: Latest US Patents, China's latest patents, Technical Efficacy Thesaurus, Application Domain, Technology Topic, Popular Technical Reports.
© 2025 PatSnap. All rights reserved.Legal|Privacy policy|Modern Slavery Act Transparency Statement|Sitemap|About US| Contact US: help@patsnap.com