Preparation method of tubular sandwich-structure CNT@Ni@Ni2(CO3)(OH)2 composite material
A composite material and sandwich technology, applied in the field of composite materials, can solve the problems of high electronic conductivity, low capacity and energy density, and large specific surface area of carbon materials, and achieve the effect of improving specific capacity, improving cycle life and high purity
- Summary
- Abstract
- Description
- Claims
- Application Information
AI Technical Summary
Problems solved by technology
Method used
Image
Examples
Embodiment 1
[0040] 1) Preparation of functionalized multi-walled carbon nanotubes
[0041] In the first step, accurately weigh 50.0 mg of original multi-walled carbon nanotubes and dissolve them in 30 mL H 2 SO 4 and 10mL HNO 3 In the mixed solution, ultrasonic dispersion. multi-walled carbon nanotubes with H 2 SO 4 and HNO 3The molar ratio of the mixed solution is 1:7; H 2 SO 4 with HNO 3 The volume ratio is 3:1;
[0042] In the second step, place a 100mL round-bottomed flask equipped with a magnetic stirrer, reflux condenser, and thermometer in an oil bath, add the ultrasonic solution, heat under reflux in an oil bath at 65°C for 5h, and cool naturally to room temperature.
[0043] In the third step, the product in the round bottom flask was collected. The product was washed, repeatedly washed with deionized water until the solution was neutral, and dried in a vacuum oven at 60° C. for 10 hours to obtain functionalized multi-walled carbon nanotubes.
[0044] 2) Synthesis of c...
Embodiment 2
[0055] The preparation method of functionalized multi-walled carbon nanotubes comprises the following steps:
[0056] Dissolving multi-walled carbon nanotubes in H 2 SO 4 and HNO 3 In the mixed solution, multi-walled carbon nanotubes and H 2 SO 4 and HNO 3 The molar ratio of the mixed solution is 1:6; H 2 SO 4 with HNO 3 The volume ratio of the solution is 3:1; ultrasonic dispersion, the time is 7 minutes; heating and reflux, the temperature is 75 ° C, the time is 4 hours, then naturally cooled to room temperature, the product is collected, and washed repeatedly with deionized water until the solution is neutral , functionalized multi-walled carbon nanotubes were obtained after vacuum drying; the temperature of vacuum drying was 70° C., and the time was 12 hours.
[0057] The preparation method of the core-shell structure CNT@Ni composite material comprises the following steps:
[0058] Accurately weigh 50 mg of functionalized carbon nanotubes, dissolve them in 50 mL ...
PUM
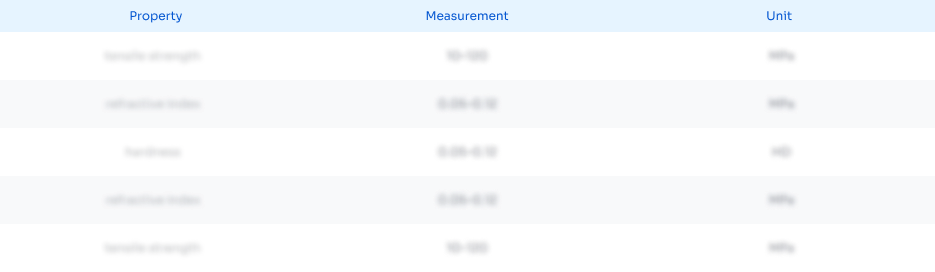
Abstract
Description
Claims
Application Information

- Generate Ideas
- Intellectual Property
- Life Sciences
- Materials
- Tech Scout
- Unparalleled Data Quality
- Higher Quality Content
- 60% Fewer Hallucinations
Browse by: Latest US Patents, China's latest patents, Technical Efficacy Thesaurus, Application Domain, Technology Topic, Popular Technical Reports.
© 2025 PatSnap. All rights reserved.Legal|Privacy policy|Modern Slavery Act Transparency Statement|Sitemap|About US| Contact US: help@patsnap.com