Intermittent vulcanized latex sponge mattress production technology
A production process, latex technology, applied in the field of natural latex sponge mattress production, can solve problems that affect the appearance of latex mattresses, cannot overcome product defects, affect product quality, etc.
- Summary
- Abstract
- Description
- Claims
- Application Information
AI Technical Summary
Problems solved by technology
Method used
Image
Examples
Embodiment 1
[0022] Embodiment one: in concrete production process, comprise the following steps:
[0023] 1) Grinding and refining the raw materials;
[0024] 2), automatic batching according to the formula through the batching system, the raw materials are composed of the following components by weight: 80 parts of natural rubber, 10 parts of synthetic rubber, 6 parts of vulcanizing agent, 3 parts of activator, 3 parts of emulsifier, 2 parts of accelerator , 2 parts of gel;
[0025] 3), mixing, pre-vulcanization, mixing natural rubber and synthetic rubber into mixed latex, adding vulcanizing agent, activator, emulsifier, accelerator and gelling agent into the mixed latex in order for stirring, mixing, pre-vulcanization treatment, Place it in a sealed tank for standby, the pre-vulcanization time is 13h, and the temperature is controlled at 28°C;
[0026] 4) Add a hardener, foam through a foaming machine, inject mold, and shape the surface. The drying temperature is 35°C and the drying t...
Embodiment 2
[0032] Embodiment two: in concrete production process, comprise the following steps:
[0033] 1) Grinding and refining the raw materials;
[0034] 2), automatically batched according to the formula through the batching system, the raw materials are composed of the following components by weight: 90 parts of natural rubber, 12 parts of synthetic rubber, 5 parts of vulcanizing agent, 4 parts of activator, 2 parts of emulsifier, 2 parts of accelerator , 3 parts of gel;
[0035] 3), mixing, pre-vulcanization, mixing natural rubber and synthetic rubber into mixed latex, adding vulcanizing agent, activator, emulsifier, accelerator and gelling agent into the mixed latex in order for stirring, mixing, pre-vulcanization treatment, Store in an airtight jar for later use.
[0036] The pre-vulcanization time is 12h, and the temperature is controlled at 26°C;
[0037] 4) Add a hardener, foam through a foaming machine, inject molding, and shape the surface. The drying temperature is 30°C...
Embodiment 3
[0043] Embodiment three: in concrete production process, comprise the following steps:
[0044] 1) Grinding and refining the raw materials;
[0045] 2), through the batching system to automatically batch according to the formula, the raw materials are composed of the following components by weight: 100 parts of natural rubber, 15 parts of synthetic rubber, 4 parts of vulcanizing agent, 6 parts of activator, 3 parts of emulsifier, and 3 parts of accelerator , 2 parts of gel;
[0046] 3), mixing, pre-vulcanization, mixing natural rubber and synthetic rubber into mixed latex, adding vulcanizing agent, activator, emulsifier, accelerator and gelling agent into the mixed latex in order for stirring, mixing, pre-vulcanization treatment, Put it in a sealed tank for standby, the pre-vulcanization time is 14h, and the temperature is controlled at 22°C;
[0047] 4) Add a hardener, foam through a foaming machine, inject mold, and shape the surface. The drying temperature is 40°C and the...
PUM
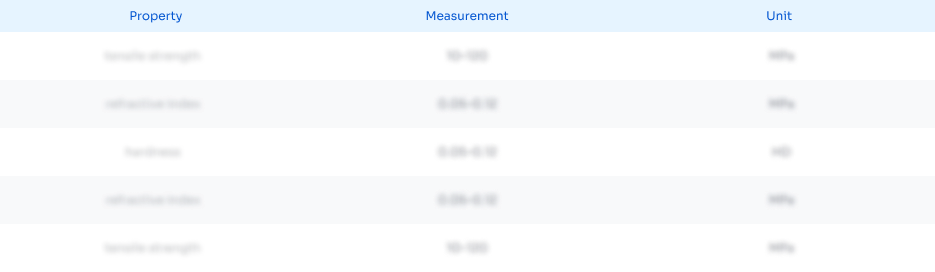
Abstract
Description
Claims
Application Information

- R&D
- Intellectual Property
- Life Sciences
- Materials
- Tech Scout
- Unparalleled Data Quality
- Higher Quality Content
- 60% Fewer Hallucinations
Browse by: Latest US Patents, China's latest patents, Technical Efficacy Thesaurus, Application Domain, Technology Topic, Popular Technical Reports.
© 2025 PatSnap. All rights reserved.Legal|Privacy policy|Modern Slavery Act Transparency Statement|Sitemap|About US| Contact US: help@patsnap.com