Tool Setting Method for Machining Large Aperture Aspherical Optical Components by Atmospheric Plasma
An optical element and plasma technology, which is applied in the field of tool setting for plasma processing large-diameter aspherical optical elements, can solve the problems of large human influence, difficult to guarantee the precision and quality of the tool, and long operation time, so as to reduce the experience, The effect of improving the precision of tool setting, the quality of assembly and adjustment, the improvement of processing quality and the stability of the process
- Summary
- Abstract
- Description
- Claims
- Application Information
AI Technical Summary
Problems solved by technology
Method used
Image
Examples
Embodiment Construction
[0023] Such as Figure 1-2 As shown, the present invention consists of an air compressor 1, an air storage tank 2, a filter 3, a solenoid valve 4, a speed control valve 5, a trigger probe 6, a pneumatic sliding table 7, a support frame 10, an adapter plate 11, and a Z-axis Guide rail 8, fixture 13 and two-dimensional adjustment platform 14 constitute. The air compressor 1, the air storage tank 2, the filter 3, the solenoid valve 4, the speed control valve 5 and the pneumatic sliding table 7 are connected through the air pipe in sequence, and the air storage tank 2 stores the energy of the gas generated by the air compressor 1 and The air pressure is stable, the filter 3 filters out the micro-particle impurities in the gas pipeline, the pneumatic sliding table 7 is installed on the support frame 10, the end of the pneumatic sliding table 7 is connected to the three-way high-precision trigger probe 6, and the trigger probe 6 moves up and down. The movement is driven by the pneu...
PUM
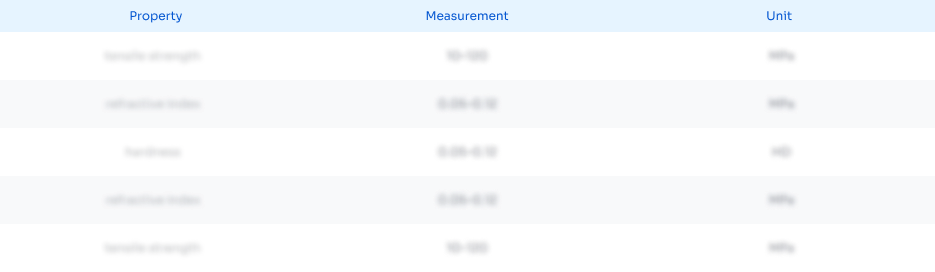
Abstract
Description
Claims
Application Information

- R&D
- Intellectual Property
- Life Sciences
- Materials
- Tech Scout
- Unparalleled Data Quality
- Higher Quality Content
- 60% Fewer Hallucinations
Browse by: Latest US Patents, China's latest patents, Technical Efficacy Thesaurus, Application Domain, Technology Topic, Popular Technical Reports.
© 2025 PatSnap. All rights reserved.Legal|Privacy policy|Modern Slavery Act Transparency Statement|Sitemap|About US| Contact US: help@patsnap.com