Continuous fiber reinforced PVC pre-dip material and preparation method thereof
A continuous fiber and prepreg technology, which is applied in the field of continuous fiber reinforced PVC prepreg and its preparation, can solve the problems of increased resin viscosity, prepreg dry yarn, and reduced fluidity, achieving simple equipment, low energy consumption, The effect of equal mechanical properties
- Summary
- Abstract
- Description
- Claims
- Application Information
AI Technical Summary
Problems solved by technology
Method used
Image
Examples
Embodiment 1
[0024] Embodiment 1: A kind of continuous glass fiber reinforced PVC prepreg is made by the following method:
[0025] (1) Take by weight 22 parts of PVC resin; 15 parts of plasticizer (8 parts of DOP, 7 parts of DBP); 3 parts of heat stabilizer (1 part of dibasic lead phosphite, 2 parts of tribasic lead phosphate ); 1.5 parts of lubricant (0.6 part of barium stearate, 0.3 part of lead stearate, 0.6 part of stearic acid); 1 part of light stabilizer uv944; 3 parts of grafting agent maleic anhydride grafted polyethylene.
[0026] (2) After accurately weighing various raw materials and additives, pour the PVC resin and plasticizer into the high-speed mixer, and then start the high-speed mixer at a low speed. After mixing at a low speed for 3 minutes, pour the heat stabilizer, lubricant, light stabilizer, and grafting agent into the high-speed mixer in sequence, and start the high-speed mixer at a low speed. After mixing for a period of time, when the temperature in the high-spee...
Embodiment 2
[0028] Embodiment 2: A kind of continuous basalt fiber reinforced PVC prepreg is made by the following method:
[0029] (1) Take by weight 25 parts of PVC resin; 18 parts of plasticizer (10 parts of DOP, 8 parts of DBP); 2 parts of heat stabilizer (0.6 part of dibasic lead phosphite, 1.4 parts of tribasic lead phosphate ); 1.5 parts of lubricant (0.6 part of barium stearate, 0.3 part of lead stearate, 0.6 part of stearic acid); 0.6 part of light stabilizer uv944; 2 parts of grafting agent maleic anhydride grafted polyethylene.
[0030] (2) After accurately weighing various raw materials and additives, pour the PVC resin and plasticizer into the high-speed mixer, and then start the high-speed mixer at a low speed. After mixing at a low speed for 3 minutes, pour the heat stabilizer, lubricant, light stabilizer, and grafting agent into the high-speed mixer in sequence, and start the high-speed mixer at a low speed. After mixing for a period of time, when the temperature in the h...
Embodiment 3
[0034]Embodiment 3: A kind of continuous carbon fiber reinforced PVC prepreg is made by the following method:
[0035] (1) Take by weight 30 parts of PVC resin; 20 parts of plasticizer (12 parts of DOP, 8 parts of DBP); 2 parts of heat stabilizer (0.6 parts of dibasic lead phosphite, 1.4 parts of tribasic lead phosphate ); 1.5 parts of lubricant (0.6 part of barium stearate, 0.3 part of lead stearate, 0.6 part of stearic acid); 0.6 part of light stabilizer uv944; 2 parts of grafting agent maleic anhydride grafted polyethylene.
[0036] (2) After accurately weighing various raw materials and additives, pour the PVC resin and plasticizer into the high-speed mixer, and then start the high-speed mixer at a low speed. After mixing at a low speed for 3 minutes, pour the heat stabilizer, lubricant, light stabilizer, and grafting agent into the high-speed mixer in sequence, and start the high-speed mixer at a low speed. After mixing for a period of time, when the temperature in the h...
PUM
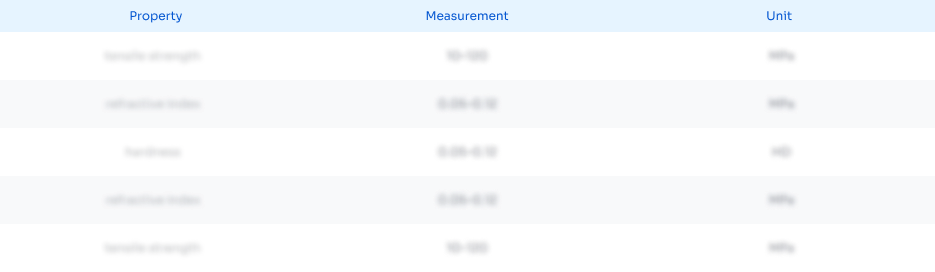
Abstract
Description
Claims
Application Information

- R&D Engineer
- R&D Manager
- IP Professional
- Industry Leading Data Capabilities
- Powerful AI technology
- Patent DNA Extraction
Browse by: Latest US Patents, China's latest patents, Technical Efficacy Thesaurus, Application Domain, Technology Topic, Popular Technical Reports.
© 2024 PatSnap. All rights reserved.Legal|Privacy policy|Modern Slavery Act Transparency Statement|Sitemap|About US| Contact US: help@patsnap.com