A vacuum coating machine for metallized film processing
A vacuum coating machine and metallized film technology, applied in vacuum evaporation coating, metal material coating process, sputtering coating, etc., can solve the problems of less film, low surface temperature of insulating film, and invariable shape, etc., to achieve Convenient feeding/receiving, avoiding unstable tension, and adjustable coating thickness
- Summary
- Abstract
- Description
- Claims
- Application Information
AI Technical Summary
Problems solved by technology
Method used
Image
Examples
Embodiment Construction
[0054] In order to further describe the present invention, it is further described below in conjunction with embodiment.
[0055] Such as figure 1 As shown, the present invention discloses a vacuum coating machine for metallized film processing, including a vacuum chamber 401 and a feeding mechanism, a coating mechanism, and a winding mechanism arranged in the vacuum chamber 401 . The feeding mechanism, the coating mechanism, and the winding mechanism are arranged in sequence from front to back according to the process flow.
[0056] Such as figure 1 As shown, the feeding mechanism includes a first lifting mechanism 101 and a feeding device. The telescopic end of the first lifting mechanism 101 cooperates with the feeding device to drive the feeding device to move up and down.
[0057] Such as figure 1 As shown, the vacuum chamber 401 includes a chamber entrance door 4011 at the entrance end and a chamber exit door 4012 at the exit end.
[0058] Such as figure 1 As shown...
PUM
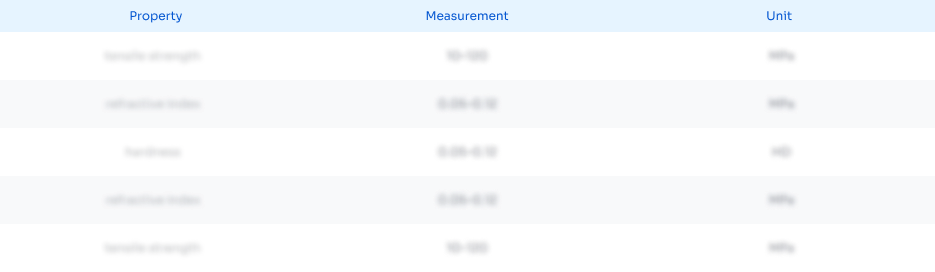
Abstract
Description
Claims
Application Information

- Generate Ideas
- Intellectual Property
- Life Sciences
- Materials
- Tech Scout
- Unparalleled Data Quality
- Higher Quality Content
- 60% Fewer Hallucinations
Browse by: Latest US Patents, China's latest patents, Technical Efficacy Thesaurus, Application Domain, Technology Topic, Popular Technical Reports.
© 2025 PatSnap. All rights reserved.Legal|Privacy policy|Modern Slavery Act Transparency Statement|Sitemap|About US| Contact US: help@patsnap.com