Glass fiber air filtration filter material treating agent and preparation method
An air filtration and glass fiber technology, applied in fiber processing, fiber type, textile and papermaking, etc., can solve the problems of poor transparency, easy moisture regain, easy yellowing of glass fibers, etc., and achieves high glass transition temperature and folding resistance. Improved, good oxidation resistance
- Summary
- Abstract
- Description
- Claims
- Application Information
AI Technical Summary
Problems solved by technology
Method used
Examples
Embodiment 1
[0023] (1) Add 298 parts of acrylic acid, 13 parts of hydroxyethyl methacrylate, and 56 parts of sodium methacrylate to the neutralization kettle, and neutralize with 50 parts of sodium hydroxide solution with a concentration of 28-30% by mass To a pH value of 3-5, the neutralizing solution is prepared; 30 parts of the neutralizing solution are released from the neutralizing tank into a plastic bucket for use; the remaining neutralizing solution in the neutralizing tank is poured into the dripping tank for use;
[0024] (2) Add 200 parts of water, 30 parts of neutralizing solution in the plastic barrel of step (1), 20 parts of isopropanol in the reaction kettle, stir, heat up to 60-65 ° C, add 2 parts of sodium persulfate and 10 parts of water Parts of prepared sodium persulfate aqueous solution, stirred, and heated to 85-90°C. Then control the temperature at 85-90°C, and add dropwise the sodium persulfate aqueous solution prepared by step (1) neutralizing liquid in the drippi...
Embodiment 2
[0027] (1) Add 300 parts of acrylic acid, 14 parts of hydroxyethyl methacrylate, and 57 parts of sodium methacrylate to the neutralization kettle, and neutralize with 55 parts of sodium hydroxide solution with a concentration of 28-30% by mass To a pH value of 3-5, the neutralizing solution is prepared; 32 parts of the neutralizing solution are released from the neutralizing tank into a plastic bucket for use; the remaining neutralizing solution in the neutralizing tank is poured into the dripping tank for use;
[0028] (2) Add 215 parts of water, 32 parts of neutralizing solution in the plastic bucket of step (1), 23 parts of isopropanol in the reaction kettle, stir, heat up to 60-65°C, add 3 parts of sodium persulfate and 13 parts of water Parts of prepared sodium persulfate aqueous solution, stirred, and heated to 85-90°C. Then control the temperature at 85-90°C, and add dropwise the aqueous solution of sodium persulfate prepared from the neutralizing liquid in the dripping...
Embodiment 3
[0031] (1) Add 302 parts of acrylic acid, 15 parts of hydroxyethyl methacrylate, and 58 parts of sodium methacrylate to the neutralization kettle, and neutralize with 60 parts of sodium hydroxide solution with a concentration of 28-30% by mass To a pH value of 3-5, a neutralizing liquid is prepared; 34 parts of neutralizing liquid are released from the neutralizing tank into a plastic bucket for use, and the remaining neutralizing liquid in the neutralizing tank is poured into a drip tank for use;
[0032] (2) Add 230 parts of water, 34 parts of neutralizing solution in the plastic barrel of step (1), 25 parts of isopropanol in the reaction kettle, stir, heat up to 60-65 ° C, add 4 parts of sodium persulfate and 15 parts of water Parts of prepared sodium persulfate aqueous solution, stirred, and heated to 85-90°C. Then control the temperature at 85-90°C, and add dropwise the sodium persulfate aqueous solution prepared by step (1) neutralizing liquid, acrylonitrile 34, 6 parts ...
PUM
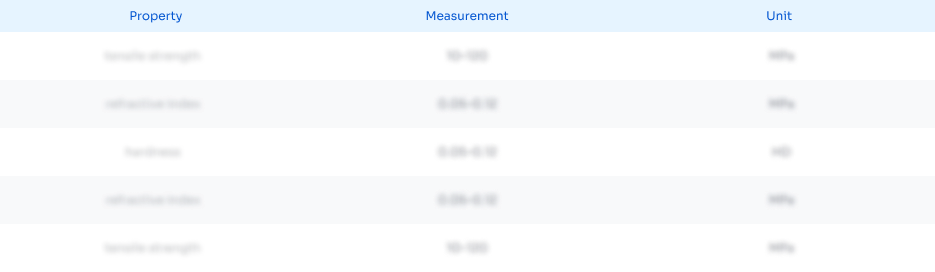
Abstract
Description
Claims
Application Information

- R&D
- Intellectual Property
- Life Sciences
- Materials
- Tech Scout
- Unparalleled Data Quality
- Higher Quality Content
- 60% Fewer Hallucinations
Browse by: Latest US Patents, China's latest patents, Technical Efficacy Thesaurus, Application Domain, Technology Topic, Popular Technical Reports.
© 2025 PatSnap. All rights reserved.Legal|Privacy policy|Modern Slavery Act Transparency Statement|Sitemap|About US| Contact US: help@patsnap.com