Integrated continuous production type clay dissociation-modification-drying method
A production method and clay technology, applied in the field of clay dissociation, can solve the problems of high cost, high energy consumption, and non-environmental protection, and achieve the effect of low cost, low energy consumption, and easy control of the process
- Summary
- Abstract
- Description
- Claims
- Application Information
AI Technical Summary
Problems solved by technology
Method used
Examples
Embodiment 1
[0021] Embodiment 1: Follow the steps below to connect and produce modified micro-nano attapulgite powder
[0022] (1) Clay pretreatment: fully mix and soak 100 mesh attapulgite with isopropanol; among them, isopropanol is twice the mass of attapulgite;
[0023] (2) Extrusion treatment: choose an intermeshing co-rotating twin-screw extruder, adjust the length-to-diameter ratio of the twin-screw to 1:32, and control the extrusion temperature to 50°C; Active agent - quaternary ammonium salt is added at a uniform speed, mixed and extruded;
[0024] (3) Drying: Heat and dry the extruded attapulgite at 80°C to remove the solvent, and at the same time recycle and reuse the used isopropanol to obtain cetyltrimethylammonium bromide ammonium bromide in a soft agglomerated state. Sexual micro-nano attapulgite powder.
Embodiment 2
[0025] Embodiment 2: Follow the steps below to connect and produce modified micro-nano attapulgite powder
[0026] (1) Clay pretreatment: fully soak 60-mesh sepiolite in water for 2 hours, and the amount of water used is twice the mass of sepiolite;
[0027] (2) Extrusion treatment: Select an intermeshing co-rotating twin-screw extruder, adjust the length-to-diameter ratio of the twin-screws to 1:46, control the extrusion temperature to 125°C, and replace the pretreated sepiolite with 3% of its mass Sexual agent - silane coupling agent is added at a uniform speed and mixed and extruded;
[0028] (3) Drying: The extruded sepiolite is heated, dried and dehydrated at 120°C to obtain micro-nano sepiolite clay powder in a soft agglomerated state.
Embodiment 3
[0029] Embodiment 3: Follow the steps below to connect and produce modified micro-nano attapulgite powder
[0030] (1) Clay pretreatment: fully soak 200-mesh dolomite-type attapulgite in N,N-dimethylformamide, the amount of which is 3 times the mass of clay;
[0031] (2) Extrusion treatment: choose an intermeshing co-rotating twin-screw extruder, adjust the length-to-diameter ratio of the twin-screw to 1:60, and control the extrusion temperature to 200°C; Modifier - stearic acid is added at a uniform speed and mixed for extrusion;
[0032] (3) Drying: heat and dry the extruded dolomite-type attapulgite at 160°C to remove the solvent, and then obtain the modified micronanoized dolomite-type attapulgite powder in a soft agglomerated state. -Dimethylformamide is recycled for reuse.
PUM
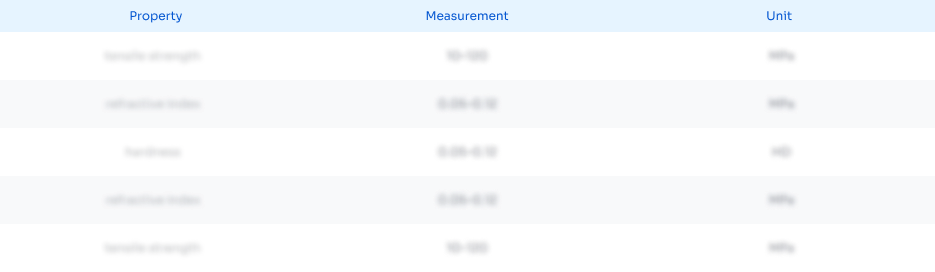
Abstract
Description
Claims
Application Information

- R&D
- Intellectual Property
- Life Sciences
- Materials
- Tech Scout
- Unparalleled Data Quality
- Higher Quality Content
- 60% Fewer Hallucinations
Browse by: Latest US Patents, China's latest patents, Technical Efficacy Thesaurus, Application Domain, Technology Topic, Popular Technical Reports.
© 2025 PatSnap. All rights reserved.Legal|Privacy policy|Modern Slavery Act Transparency Statement|Sitemap|About US| Contact US: help@patsnap.com