Wood veneer treatment method and reconstituted wood
A processing method and veneer technology, which is applied in wood compression, wood processing equipment, other plywood/plywood equipment, etc., can solve the problem of warping and deformation of recombined wood, long time of dipping of wooden veneer, and the amount of dipping and uneven pavement, to reduce the risk of cracking, improve density uniformity, reduce initial stress and pressing pressure
- Summary
- Abstract
- Description
- Claims
- Application Information
AI Technical Summary
Problems solved by technology
Method used
Image
Examples
preparation example Construction
[0031] In the preparation method of the above-mentioned recombined wood provided by the present invention, firstly, the treated veneer is dipped in glue. Wherein, the glue used for dipping is preferably phenolic resin impregnated glue; the solid content of the glue is preferably 20 to 25wt%; the dipping method is preferably normal pressure dipping; the dipping time is preferably 5-60 min, more preferably 10-20 min; the dipping amount of the dipping is preferably controlled at 15-30 wt%, more preferably 16-25 wt%, and most preferably 20±2 wt%. In the present invention, it is preferable to dry the treated veneer before dipping, so as to reduce the moisture content of the veneer. The drying temperature is preferably 80-120°C; the moisture content of the dried veneer is preferably 8-12%.
[0032] After dipping, drain the liquid, and enter the next process when there is no obvious liquid dripping, that is, press the veneer after dipping. In the present invention, the pressed dens...
Embodiment 1
[0037] wood veneer treatment
[0038] 1) Rotary cutting: using a rotary cutting machine to cut Russian poplar into wooden veneers, the thickness of the veneer is 1.3±0.1mm, the width is 250mm, the length is 650mm, and the moisture content is 130±10%;
[0039] 2), roll pressing:
[0040] Put the wooden veneer into the roller press according to the direction of its fiber transverse grain for rolling. The rolling process is as follows: figure 1 as shown, figure 1It is a schematic diagram of the rolling process of the wooden veneer provided in Example 1 of the present invention, wherein, G1 is the upper roll, G2 is the lower roll, 1 is the veneer before rolling, 2 is the veneer after rolling, the upper and lower rolls G1 and The main body of G2 is a cylindrical smooth cylinder with no teeth and threads on the surface of the cylinder. In this embodiment, the gap between the pressure rollers G1 and G2 is controlled to be 1±0.1 mm, the rotational speed of the lower roller is 20 r / ...
Embodiment 2
[0042] Preparation of recombinant wood
[0043] 1) Drying before gluing: Put the treated veneer obtained in Example 1 into a mesh belt dryer for drying treatment at a temperature of 80-120°C to make the moisture content within 8-12%;
[0044] 2), dipping: prepare water-based low molecular weight phenolic resin dipping solution, the specific method is: phenol, methanol and sodium hydroxide are synthesized according to the molar ratio of 1:1.8:0.2 phenolic resin dipping solution, the solid content of the glue is 40wt %, the viscosity at 25°C is 20S, and the pH is 11; dilute the glue solution to a solid content of 20-25wt%, adopt the method of normal pressure dipping, the dipping time is 10min, and the dipping amount is controlled at 20±2wt of the veneer quality %. After the dipping is completed, take out the wood veneer, drain the liquid, and enter the next process when there is no obvious liquid dripping;
[0045] 3) Drying after gluing: Put the dipped veneer into a mesh belt...
PUM
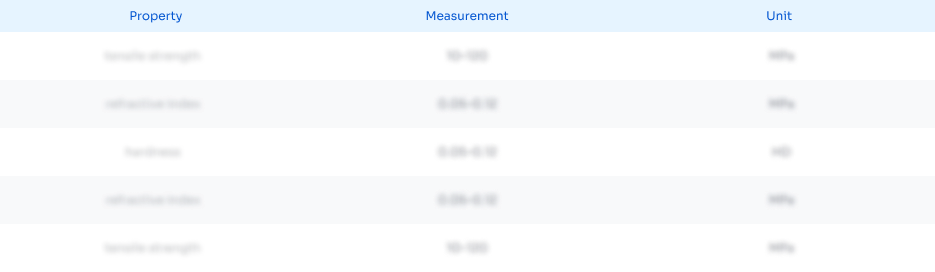
Abstract
Description
Claims
Application Information

- Generate Ideas
- Intellectual Property
- Life Sciences
- Materials
- Tech Scout
- Unparalleled Data Quality
- Higher Quality Content
- 60% Fewer Hallucinations
Browse by: Latest US Patents, China's latest patents, Technical Efficacy Thesaurus, Application Domain, Technology Topic, Popular Technical Reports.
© 2025 PatSnap. All rights reserved.Legal|Privacy policy|Modern Slavery Act Transparency Statement|Sitemap|About US| Contact US: help@patsnap.com