Catalyst containing modified molecular sieve and preparation method thereof
A molecular sieve and catalyst technology, which is applied in the field of catalytic cracking catalysts, can solve problems such as insufficient ability to resist heavy metal pollution, large rare earth precipitate particles, and contact
- Summary
- Abstract
- Description
- Claims
- Application Information
AI Technical Summary
Problems solved by technology
Method used
Image
Examples
Embodiment 1
[0048] Mix 2g of citric acid, 2.48mL of rare earth nitrate and 75mL of deionized water to form a homogeneous solution, then add 2g of ammonium oxalate and stir for 15 minutes to form a rare earth-containing precipitate slurry CD-1.
Embodiment 2
[0050] Mix 2g of ethanol, 2.48mL of rare earth nitrate and 75mL of deionized water to form a uniform solution, then add 2g of ammonium oxalate and stir for 15 minutes to form a rare earth-containing precipitate slurry CD-2.
Embodiment 3
[0058] (1) Mix 16 g of citric acid, 4 g of ethylene glycol, 54 g of yttrium nitrate and 1 L of deionized water to form a uniform solution, then add 100 g of ammonium oxalate, and stir for 15 minutes to form a yttrium-containing precipitate slurry.
[0059] (2) Add the precipitate slurry formed in step (1) into the self-made yttrium-containing Y-type molecular sieve slurry Y-1, stir at a temperature of 55°C for 10 minutes, filter, wash with water, and filter the cake at 600°C and 100% steam Calcined under atmosphere for 2 hours. The modified molecular sieve Z-1 was obtained.
[0060] Add 600 g (dry basis) of molecular sieve Z-1 into 1.2 L of deionized water, and perform sand milling to obtain molecular sieve slurry Z-1J. Mix 619g of alumina sol, 1499g of kaolin, and 2.2L of water for beating, then add molecular sieve slurry Z-1J, continue stirring for 30 minutes, homogenize, spray dry and form, roast, wash with water, and dry to obtain catalyst C-1 of the present invention.
PUM
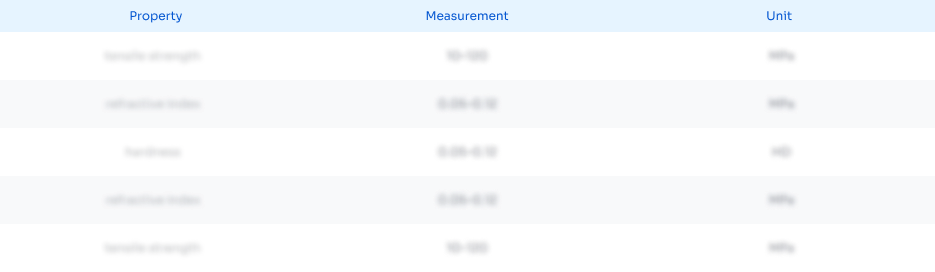
Abstract
Description
Claims
Application Information

- R&D Engineer
- R&D Manager
- IP Professional
- Industry Leading Data Capabilities
- Powerful AI technology
- Patent DNA Extraction
Browse by: Latest US Patents, China's latest patents, Technical Efficacy Thesaurus, Application Domain, Technology Topic, Popular Technical Reports.
© 2024 PatSnap. All rights reserved.Legal|Privacy policy|Modern Slavery Act Transparency Statement|Sitemap|About US| Contact US: help@patsnap.com