System for detecting deformation in cushion pad and method for manufacturing same
A manufacturing method and technology of cushioning pads, applied in the field of deformed systems, can solve problems such as difficulty in disposing the surface of cushioning materials, deterioration of detection accuracy, foreign body sensation, etc., and achieve good riding experience, simple manufacturing, and less peeling.
- Summary
- Abstract
- Description
- Claims
- Application Information
AI Technical Summary
Problems solved by technology
Method used
Image
Examples
manufacture example 1
[0065] Manufacturing example 1 Synthesis of isocyanate-terminated prepolymer A
[0066] Add 85.2 parts by mass of polyol A (polyoxypropylene glycol with propylene oxide added to glycerol as an initiator, OH value 56, functional group number 3) in the reaction vessel, and carry out dehydration under reduced pressure for 1 hour while stirring . Thereafter, the inside of the reaction container was replaced with nitrogen. Next, 14.8 parts by mass of toluene diisocyanate (manufactured by Mitsui Chemicals, Inc., 2,4-type = 100%, NCO% = 48.3%) was added to the reaction container, and the reaction was carried out for 3 hours while keeping the temperature in the reaction container at 80°C. Whereas, isocyanate-terminated prepolymer A (NCO%=3.58%) was synthesized.
manufacture example 2
[0067] Manufacturing example 2 Synthesis of isocyanate-terminated prepolymer B
[0068] 81.2 parts by mass of polyol C (polyoxypropylene glycol to which propylene oxide was added using pentaerythritol as an initiator, OH value 75, number of functional groups 3) was added to a reaction vessel, and vacuum dehydration was performed for 1 hour while stirring. Thereafter, the inside of the reaction container was replaced with nitrogen. Next, 18.8 parts by mass of toluene diisocyanate (manufactured by Mitsui Chemicals, Inc., 2,4-type = 100%, NCO% = 48.3%) was added to the reaction container, and the reaction was carried out for 3 hours while keeping the temperature in the reaction container at 80°C. Whereas, isocyanate-terminated prepolymer B (NCO%=4.55%) was synthesized.
Embodiment 1
[0070] Next, a neodymium-based filler (manufactured by Aichi Steel Works, MF-15P, average Particle size: 133 μm) 631.2 parts by mass to prepare a filler dispersion. This filler dispersion was defoamed under reduced pressure, and 100.0 parts by mass of the above-mentioned prepolymer A, which had also been defoamed under reduced pressure, was added, and mixed and defoamed using a planetary mixer (manufactured by Shinki Co., Ltd.). The reaction liquid was dropped onto a release-treated PET film having a spacer of 1.0 mm, and adjusted to a thickness of 1.0 mm using a nip roller. Thereafter, as a bias treatment of the magnetic filler, the magnetic filler was precipitated by standing at room temperature for 30 minutes. Thereafter, curing was performed at 80° C. for 1 hour to obtain a filler-dispersed polyurethane elastomer. A magnetic elastic body was obtained by magnetizing the obtained elastic body at 1.3 T in a magnetization device (manufactured by Denki Magnetic Industry Co., ...
PUM
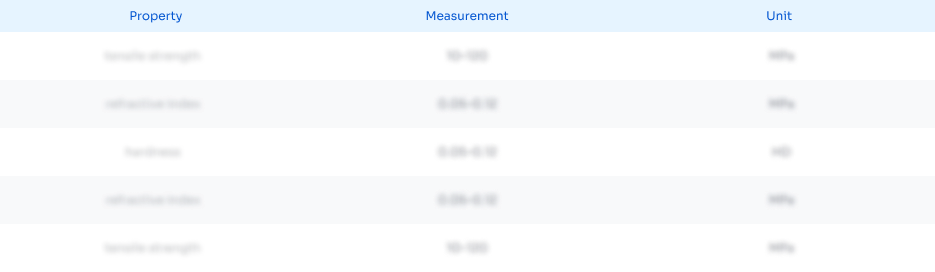
Abstract
Description
Claims
Application Information

- Generate Ideas
- Intellectual Property
- Life Sciences
- Materials
- Tech Scout
- Unparalleled Data Quality
- Higher Quality Content
- 60% Fewer Hallucinations
Browse by: Latest US Patents, China's latest patents, Technical Efficacy Thesaurus, Application Domain, Technology Topic, Popular Technical Reports.
© 2025 PatSnap. All rights reserved.Legal|Privacy policy|Modern Slavery Act Transparency Statement|Sitemap|About US| Contact US: help@patsnap.com