Refining method for controlling brittle inclusions in bearing steel
A technology of brittle inclusions and bearing steel, applied in the field of iron and steel metallurgy, can solve the problems of difficulty and effective control, achieve good desulfurization ability, good melting performance, and solve the effect of difficult slag removal
- Summary
- Abstract
- Description
- Claims
- Application Information
AI Technical Summary
Problems solved by technology
Method used
Image
Examples
Embodiment 1
[0021] Embodiment 1: The refining method for controlling brittle inclusions in bearing steel adopts the following specific processes.
[0022] 1. LF refining process: including tapping alloying to LF treatment position pre-deoxidation slagging process and LF treatment process.
[0023] (1) The process of tapping alloying to LF treatment position pre-deoxidation and slag formation: the temperature of molten steel at the end of converter smelting is 1600°C, and 7kg / t steel is added in the later stage of tapping. The main components of refining slag are: CaO 45%, SiO 2 2%, Al 2 o 3 45%; the flow rate of ladle bottom blowing during tapping is controlled at 3.5L / min•t -1 At the end of tapping, the sliding plate is used to stop the slag to control the amount of slag ≤ 3kg / t of steel, and 20kg of aluminum particles are added to the molten steel to deoxidize the slag to reduce the oxidation of the slag; after tapping, the bottom blowing flow rate of the ladle is controlled to 0.35...
Embodiment 2
[0027] Embodiment 2: The refining method for controlling brittle inclusions in bearing steel adopts the following specific processes.
[0028] 1. LF refining process: including tapping alloying to LF treatment position pre-deoxidation slagging process and LF treatment process.
[0029] (1) The process of tapping alloying to LF treatment position pre-deoxidation and slag formation: the temperature of molten steel at the end of converter smelting is 1650°C, and 10kg / t steel is added in the later stage of tapping. The main components of refining slag are: CaO 60%, SiO 2 1.5%, Al 2 o 3 35%; the flow rate of ladle bottom blowing during tapping is controlled at 3.2NL / min•t -1 At the end of tapping, the sliding plate is used to stop the slag to control the amount of slag ≤ 3kg / t of steel, and 40kg of aluminum particles are added to the molten steel to deoxidize the slag to reduce the oxidation of the slag; after tapping, the bottom blowing flow rate of the ladle is controlled to ...
Embodiment 3
[0033] Embodiment 3: The refining method for controlling brittle inclusions in bearing steel adopts the following specific processes.
[0034] 1. LF refining process: including the pre-deoxidation slagging process to the LF treatment position and the LF treatment process.
[0035] (1) The process of tapping alloying to LF treatment position pre-deoxidation and slag formation: the temperature of molten steel at the end of converter smelting is 1620°C, and 8kg / t of refining slag is added in the later stage of tapping. The main components of refining slag are: CaO 50%, SiO 2 3%, Al 2 o 3 45%; the flow rate of ladle bottom blowing during tapping is controlled at 3.0L / min•t -1 At the end of tapping, the sliding plate is used to stop the slag to control the amount of slag ≤ 3kg / t of steel, and 30kg of aluminum particles are added to the molten steel to strongly deoxidize the slag and reduce the oxidation of the slag; after tapping, the bottom blowing flow rate of the ladle is co...
PUM
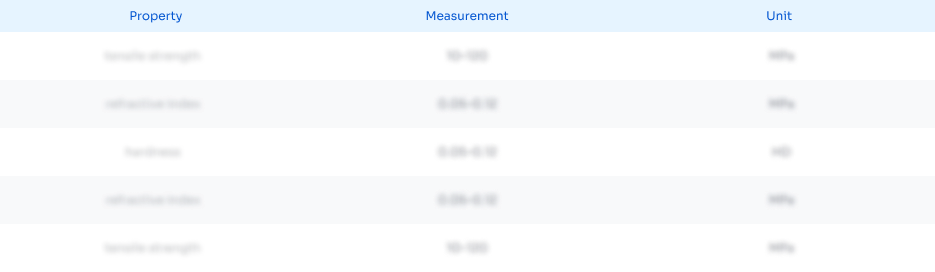
Abstract
Description
Claims
Application Information

- Generate Ideas
- Intellectual Property
- Life Sciences
- Materials
- Tech Scout
- Unparalleled Data Quality
- Higher Quality Content
- 60% Fewer Hallucinations
Browse by: Latest US Patents, China's latest patents, Technical Efficacy Thesaurus, Application Domain, Technology Topic, Popular Technical Reports.
© 2025 PatSnap. All rights reserved.Legal|Privacy policy|Modern Slavery Act Transparency Statement|Sitemap|About US| Contact US: help@patsnap.com