Recovery method of by-product sodium chloride in production process of polyphenylene sulfide
A technology of production process and recovery method, applied in the field of polymer engineering, can solve the problems of incapable of industrial use of salt, removal of by-products, etc., and achieve the effect of low energy consumption in steps and smooth production
- Summary
- Abstract
- Description
- Claims
- Application Information
AI Technical Summary
Problems solved by technology
Method used
Image
Examples
Embodiment 1
[0025] Take by weighing 1700Kg of crystalline sodium sulfide pentahydrate, 1430Kg of p-dichlorobenzene, 175Kg of catalyst lithium chloride, 7000Kg of solvent N-methylpyrrolidone (wherein 2000Kg is used for dissolving p-dichlorobenzene, and 5000Kg is used for dehydration), polymerized in the reactor reaction. The pre-polymerization temperature is 225±2°C, and the time is 45 minutes; the polymerization temperature is 265±2°C, and the time is 150 minutes. After the polymerization reaction is completed, the temperature of the mixed slurry is cooled to 90° C., and filtered with a continuous centrifuge to obtain filter cake and by-product slurry. Wash the filter cake with 8000Kg deionized water to obtain PPS wet material and washing water, and dry the PPS wet material in a dryer to obtain the finished PPS product. Mix the washing water with the above-mentioned filtrate, and then settle in the settling tank, and the settling time is 30 minutes. The supernatant in the settling tank ...
Embodiment 2
[0027] Take by weighing 1500Kg of crystalline sodium sulfide pentahydrate, 1250Kg of p-dichlorobenzene, 165Kg of catalyst lithium chloride, 5700Kg of solvent N-methylpyrrolidone (wherein 1200Kg is used for dissolving p-dichlorobenzene, and 4500Kg is used for dehydration), and polymerize in the reactor reaction. The pre-polymerization temperature is 223±2°C, and the time is 60 minutes; the polymerization temperature is 262±2°C, and the time is 180 minutes. After the polymerization reaction is completed, the temperature of the mixed slurry is cooled to 80° C., and filtered with a continuous centrifuge to obtain filter cake and by-product slurry. Wash the filter cake with 7500Kg deionized water to obtain PPS wet material and washing water, and dry the PPS wet material in a dryer to obtain the finished PPS product. The washing water and the above-mentioned filtrate were mixed, and then settled in the settling tank, and the settling time was 45 minutes. The supernatant in the set...
Embodiment 3
[0029]Take by weighing 1350Kg of crystalline sodium sulfide pentahydrate, 1230Kg of p-dichlorobenzene, 140Kg of catalyst lithium chloride, 5500Kg of solvent N-methylpyrrolidone (wherein 1000Kg is used for dissolving p-dichlorobenzene, and 4500Kg is used for dehydration), polymerized in the reactor reaction. The pre-polymerization temperature is 225±2°C, and the time is 45 minutes; the polymerization temperature is 265±2°C, and the time is 150 minutes. After the polymerization reaction, the temperature of the mixed slurry was cooled to 85° C., and filtered with a continuous centrifuge to obtain filter cake and by-product slurry. Wash the filter cake with 7500Kg deionized water to obtain PPS wet material and washing water, and dry the PPS wet material in a dryer to obtain the finished PPS product. The washing water and the above-mentioned filtrate were mixed, and then settled in the settling tank, and the settling time was 60 minutes. The supernatant in the settling tank is fi...
PUM
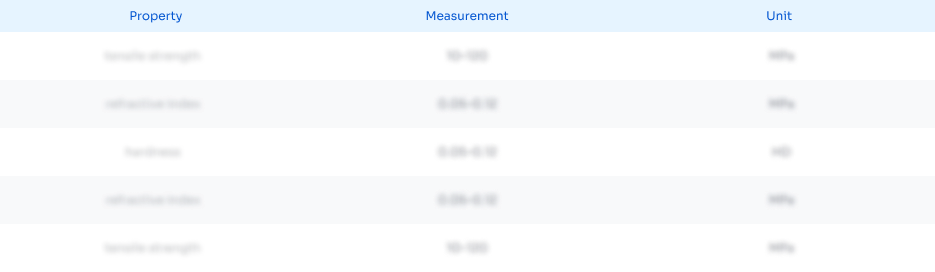
Abstract
Description
Claims
Application Information

- R&D
- Intellectual Property
- Life Sciences
- Materials
- Tech Scout
- Unparalleled Data Quality
- Higher Quality Content
- 60% Fewer Hallucinations
Browse by: Latest US Patents, China's latest patents, Technical Efficacy Thesaurus, Application Domain, Technology Topic, Popular Technical Reports.
© 2025 PatSnap. All rights reserved.Legal|Privacy policy|Modern Slavery Act Transparency Statement|Sitemap|About US| Contact US: help@patsnap.com