Selective laser sintering and melting equipment
A technology of laser sintering and melting equipment, which is applied to the improvement of process efficiency, additive manufacturing, additive processing, etc., can solve the problems of consumption of inert gas and increase of production cost, and achieve the effect of avoiding lens overheating and reducing production cost
- Summary
- Abstract
- Description
- Claims
- Application Information
AI Technical Summary
Problems solved by technology
Method used
Image
Examples
Embodiment Construction
[0022] figure 1 It is a structural schematic diagram of the present invention. As shown in the figure, the selective laser sintering and melting equipment of this embodiment includes a sealed molding chamber, a laser vibrating mirror 7 arranged outside the sealed molding chamber, and a laser vibrating mirror 7 arranged on the surface of the sealed molding chamber for making the laser vibrating mirror 7 The projected laser enters the lens 9 in the sealed molding chamber, the part processing platform 10 arranged in the sealed molding chamber, the powder spreading scraper 25 for laying powder on the processing platform, fixed on the inner wall of the sealed molding chamber and An annular air curtain device 8 corresponding to the lens 9 and a gas source for providing gas to the annular air curtain device 8; the annular air curtain device 8 is provided with a central hole for the laser to pass through, surrounding The annular gas channel provided in the central hole, the air curta...
PUM
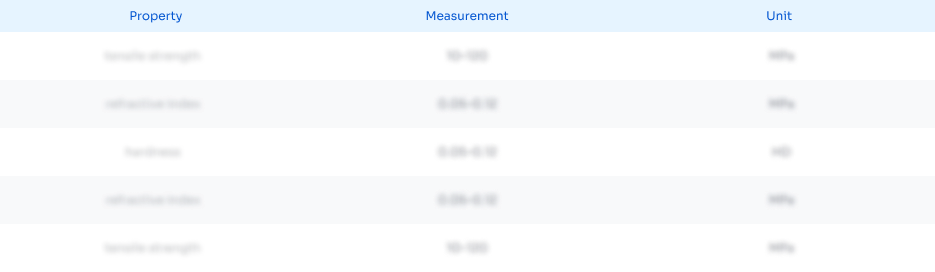
Abstract
Description
Claims
Application Information

- R&D Engineer
- R&D Manager
- IP Professional
- Industry Leading Data Capabilities
- Powerful AI technology
- Patent DNA Extraction
Browse by: Latest US Patents, China's latest patents, Technical Efficacy Thesaurus, Application Domain, Technology Topic, Popular Technical Reports.
© 2024 PatSnap. All rights reserved.Legal|Privacy policy|Modern Slavery Act Transparency Statement|Sitemap|About US| Contact US: help@patsnap.com