Non-transfer organic silicon modified acrylate parting agent and preparation method thereof
An acrylate and organosilicon technology, applied in the field of organosilicon modified acrylate release agent and its preparation, can solve problems such as transfer, and achieve the effects of simple synthesis process, enhanced blending compatibility and low cost
- Summary
- Abstract
- Description
- Claims
- Application Information
AI Technical Summary
Problems solved by technology
Method used
Examples
Embodiment 1
[0044] Weigh 60g of ethyl acetate, 0.12g of AIBN, 2g of glycidyl methacrylate, 20g of methyl methacrylate, and 10g of butyl acrylate, add them into the reaction kettle, raise the temperature to 80°C, and react for 3h. 7.76 g of amino-terminated siloxane and 0.12 g of triethylamine were added dropwise for 2 hours, followed by a heat preservation reaction for 6 hours to obtain a silicone-modified acrylate. Add 0.3g of chlorinated polyolefin, 0.6g of SBS, and stir at room temperature for 30min to prepare a silicone-modified acrylate release agent.
[0045] The silicone-modified acrylate release agent prepared in Example 1 was applied in the field of PE protective film, and the adhesion retention rate of the pressure-sensitive adhesive was 99%.
Embodiment 2
[0047] Weigh 50g of ethyl acetate, 0.12g of AIBN, 5g of glycidyl methacrylate, 20g of methyl methacrylate, and 10g of butyl acrylate, add them into the reaction kettle, raise the temperature to 80°C, and react for 3h. Add 19.76 g of amino-terminated siloxane and 0.12 g of triethylamine dropwise, add dropwise for 2 hours, and keep warm for 6 hours to prepare silicone-modified acrylate. Add 0.3g of chlorinated polyolefin, 0.6g of SBS, and stir at room temperature for 30min to prepare a silicone-modified acrylate release agent.
[0048] The silicone-modified acrylate release agent prepared in Example 2 is applied in the field of PE protective film, and the adhesion retention rate of the pressure-sensitive adhesive is 100%.
Embodiment 3
[0050] Weigh 40g of ethyl acetate, 0.12g of AIBN, 8g of glycidyl methacrylate, 26g of methyl methacrylate, and 12g of butyl acrylate, add them into the reaction kettle, raise the temperature to 80°C, and react for 3h. 13.76 g of amino-terminated siloxane and 0.12 g of triethylamine were added dropwise for 2 hours, followed by a heat preservation reaction for 6 hours to obtain a silicone-modified acrylate. Add 0.3g of chlorinated polyolefin, 0.6g of SBS, and stir at room temperature for 30min to prepare a silicone-modified acrylate release agent.
[0051] The silicone-modified acrylate release agent prepared in Example 3 is applied in the field of PE protective film, and the adhesion retention rate of the pressure-sensitive adhesive is 100%.
PUM
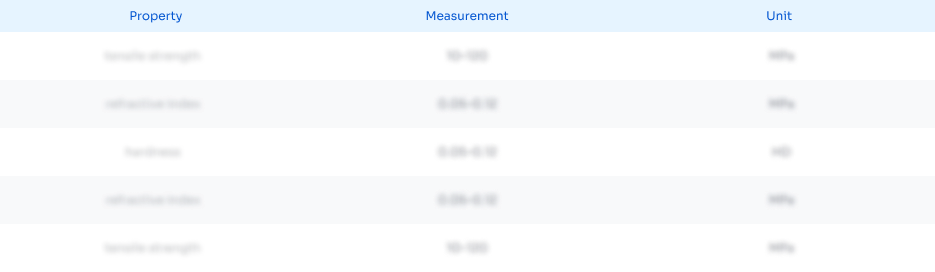
Abstract
Description
Claims
Application Information

- R&D Engineer
- R&D Manager
- IP Professional
- Industry Leading Data Capabilities
- Powerful AI technology
- Patent DNA Extraction
Browse by: Latest US Patents, China's latest patents, Technical Efficacy Thesaurus, Application Domain, Technology Topic, Popular Technical Reports.
© 2024 PatSnap. All rights reserved.Legal|Privacy policy|Modern Slavery Act Transparency Statement|Sitemap|About US| Contact US: help@patsnap.com