Method for spheroidizing heat treatment of eutectic silicon in eutectic aluminium-silicon alloy
A heat treatment method, eutectic aluminum-silicon technology, which is applied in the field of metal heat treatment, can solve the problems of improving the strength and toughness of eutectic aluminum-silicon alloy, the eutectic silicon shape is not in the best state, and the deterioration effect is poor.
- Summary
- Abstract
- Description
- Claims
- Application Information
AI Technical Summary
Problems solved by technology
Method used
Image
Examples
Embodiment 1
[0021] Example 1: Eutectic Al-Si alloy annealed at 577°C for 1 hour
[0022] An Al-11.7wt.% Si eutectic aluminum-silicon alloy was smelted in a graphite crucible using a well-type electric furnace, and the alloy liquid was poured into a metal mold to obtain a eutectic aluminum-silicon alloy sample with a diameter of 10 mm. The samples were placed in a tubular annealing furnace at 577°C for 1 hour of spheroidizing annealing treatment. After annealing, the samples were taken out for air cooling. The microstructure of the eutectic Al-Si alloy after spheroidizing annealing for 1 hour is as follows: image 3 As shown in (b), it can be seen that after annealing at 577°C for 1 hour, about 30% of the eutectic silicon has been spheroidized.
Embodiment 2
[0023] Example 2: Eutectic Al-Si alloy annealed at 577°C for 2 hours
[0024] An Al-11.7wt.% Si eutectic aluminum-silicon alloy was smelted in a graphite crucible using a well-type electric furnace, and the alloy liquid was poured into a metal mold to obtain a eutectic aluminum-silicon alloy sample with a diameter of 10 mm. The samples were respectively placed in a tubular annealing furnace at 577°C for 2 hours of spheroidizing annealing treatment. After annealing, the samples were taken out for air cooling. The microstructure of the eutectic Al-Si alloy after spheroidizing annealing for 1 hour is as follows: image 3 As shown in (c), it can be seen that after annealing at 577°C for 2 hours, about 50% of the eutectic silicon has been spheroidized.
Embodiment 3
[0025] Example 3: Eutectic Al-Si alloy annealed at 577°C for 3 hours
[0026] An Al-11.7wt.% Si eutectic aluminum-silicon alloy was smelted in a graphite crucible using a well-type electric furnace, and the alloy liquid was poured into a metal mold to obtain a eutectic aluminum-silicon alloy sample with a diameter of 10 mm. The samples were respectively placed in a tubular annealing furnace at 577°C for 3 hours of spheroidizing annealing treatment. After annealing, the samples were taken out for air cooling. The microstructure of the eutectic Al-Si alloy after spheroidizing annealing for 1 hour is as follows: image 3 As shown in (d), it can be seen that after annealing at 577°C for 3 hours, about 95% of the eutectic silicon has been spheroidized.
PUM
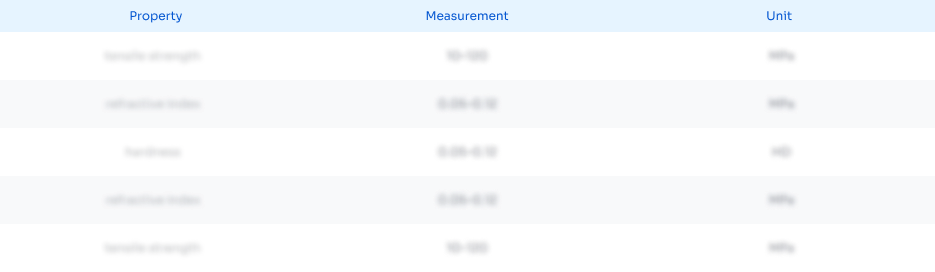
Abstract
Description
Claims
Application Information

- Generate Ideas
- Intellectual Property
- Life Sciences
- Materials
- Tech Scout
- Unparalleled Data Quality
- Higher Quality Content
- 60% Fewer Hallucinations
Browse by: Latest US Patents, China's latest patents, Technical Efficacy Thesaurus, Application Domain, Technology Topic, Popular Technical Reports.
© 2025 PatSnap. All rights reserved.Legal|Privacy policy|Modern Slavery Act Transparency Statement|Sitemap|About US| Contact US: help@patsnap.com