Method for separating disulfur dichloride in preparation process of high-purity ethyl chloride
A technology of ethyl chloride and preparation process, applied in the field of separation and purification of organic compounds, can solve the problems of high production and operation cost, large amount of distillation residue, long production cycle, etc., and achieves reduction of waste water treatment cost and comprehensive economic benefits Huge and beneficial effect
- Summary
- Abstract
- Description
- Claims
- Application Information
AI Technical Summary
Problems solved by technology
Method used
Image
Examples
Embodiment 1
[0031] The process of separating dichlorodisulfide is as follows figure 1 .
[0032] 1) Put 1000kg of crude chlorine in the rectification tower kettle, control the negative pressure at -0.098MPa, reflux ratio 4:2, and slowly raise the temperature with hot water. The size of the distillation tower is Ф400×6000mm, and the material is 316L stainless steel lined with fluorine. A digital display bimetal corrosion-resistant thermometer is installed in the tower kettle, which extends into the material.
[0033] 2) When the tower kettle temperature tower Total reflux at <55℃; when 55℃≦tower temperature≦70℃, collect yellow-red fractions as dichlorodisulfide (gas chromatographic detection content: 99.1%); when 70℃ <Temperature of tower bottom ≦83℃, the collected transitional fraction is returned to tower bottom; from the thermometer showing 83.1℃, that is 83℃ <The distillate collected when the tower kettle temperature≦93°C is refined ethyl chloride (gas chromatography detection content: 99....
Embodiment 2
[0037] 1) Put 1000kg of crude chlorine in the rectification tower kettle, control the negative pressure at -0.099MPa, reflux ratio 4:2, and slowly raise the temperature with hot water. The rectification equipment is the same as in Example 1.
[0038] 2) When the tower kettle temperature tower Total reflux at <55℃; when 55℃≦tower temperature≦70℃, collect yellow-red fractions as dichlorodisulfide (content: 99.2%); when 70℃ <Temperature of tower bottom ≦83℃, the collected transitional fraction is returned to the tower bottom; from the thermometer showing 83.2℃, that is when 83℃ <The distillate collected when the tower kettle temperature≦93°C is refined ethyl chloride (content: 99.67%).
[0039] 3) After the rectification is completed, the temperature is reduced to 40°C, and then a small amount of solid sulfur is filtered out, which is used as a by-product after refining; a small amount of residue is treated separately.
Embodiment 3
[0041] 1. Put 1000kg of crude chlorine in the rectification tower kettle, control the negative pressure at -0.1MPa, reflux ratio 4:2, and slowly heat up with hot water. The rectification equipment is the same as in Example 1.
[0042] 2. When the tower kettle temperature tower Total reflux at <55℃; when 55℃≦tower temperature≦70℃, collect yellow-red fractions as dichlorodisulfide (content: 99.4%); when 70℃
[0043] 3. After the rectification is completed, the temperature is reduced to 40°C, and then a small amount of solid sulfur is filtered out, which is used as a by-product after refining; a small amount of residual liquid is treated separately.
PUM
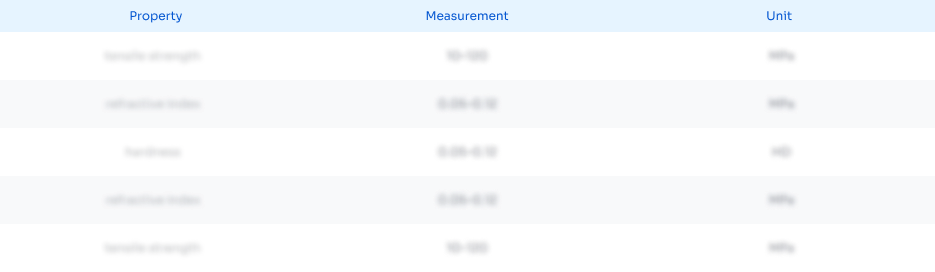
Abstract
Description
Claims
Application Information

- Generate Ideas
- Intellectual Property
- Life Sciences
- Materials
- Tech Scout
- Unparalleled Data Quality
- Higher Quality Content
- 60% Fewer Hallucinations
Browse by: Latest US Patents, China's latest patents, Technical Efficacy Thesaurus, Application Domain, Technology Topic, Popular Technical Reports.
© 2025 PatSnap. All rights reserved.Legal|Privacy policy|Modern Slavery Act Transparency Statement|Sitemap|About US| Contact US: help@patsnap.com