Method of recycling impregnated sludge carbon to catalytically gasify and recycling sludge carbon for secondary conversion of tar
A secondary conversion and sludge charcoal technology, applied in pyrolysis treatment of sludge, tar processing through heat treatment, coke oven, etc., can solve the problems of reducing energy transmission efficiency, reducing gasification rate, equipment corrosion, etc., to achieve Energy and resource utilization, overcoming easy deactivation, and efficient pyrolysis conversion effects
- Summary
- Abstract
- Description
- Claims
- Application Information
AI Technical Summary
Problems solved by technology
Method used
Examples
Embodiment 1
[0023] First, 70g of urban sewage treatment plant sludge is dried and crushed to a particle size of about 1-2mm, and the moisture content is lower than 1wt%. 2 After evacuating the air, start heating, and raise the temperature to 800°C at a heating rate of 20°C / min and keep it for 90min. Pyrolysis produces pyrolysis gas, pyrolysis liquid and sludge pyrolysis carbon; gas products are collected in a gas cabinet; pyrolysis liquid is separated by standing to obtain wood vinegar and tar products; sludge pyrolysis carbon accounts for about 44wt of raw materials %, can be reused as a catalyst. The sludge pyrolytic carbon was impregnated in the pre-prepared 0.5mol / L Ni(NO 3 ) 2 In the solution, immerse in a shaker (180r / min) for 3 days, then suction filter, put into an oven (105°C) and dry (24h), and the moisture content is less than 1wt%. Before the experiment, the impregnated sludge charcoal was put into a tube furnace with a nitrogen atmosphere, and the temperature was programme...
Embodiment 2
[0026] First, 70g of sludge from urban sewage treatment plants was dried and crushed to a particle size of about 1-2mm. 2 After evacuating the air, start heating, and raise the temperature to 800°C at a heating rate of 20°C / min and keep it for 90min. Pyrolysis produces pyrolysis gas, pyrolysis liquid and sludge pyrolysis carbon; the gas products are collected in a gas cabinet; the pyrolysis liquid is separated by standing to obtain wood vinegar and tar products; sludge pyrolysis carbon accounts for about 44% of the raw material %, can be reused as a catalyst. The sludge pyrolytic carbon was impregnated in the pre-prepared 0.5mol / L Fe(NO 3 ) 3 In the solution, immerse in a shaker (180r / min) for 3 days, then filter with suction, and put it into an oven (105°C) for drying (24h). Before the experiment, the impregnated sludge charcoal was placed in a tube furnace with an inert gas atmosphere, and the temperature was programmed to rise to 800°C at a rate of 20°C / min and roasted f...
PUM
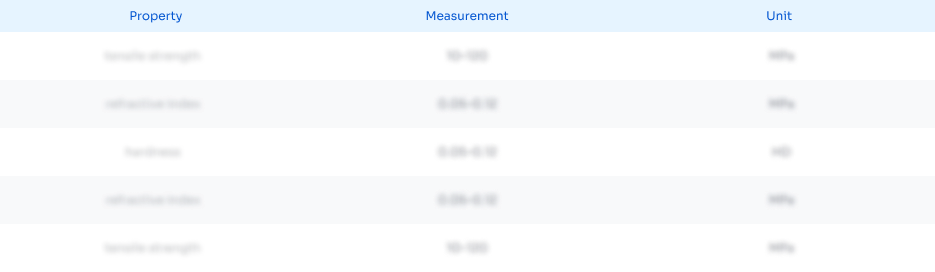
Abstract
Description
Claims
Application Information

- R&D Engineer
- R&D Manager
- IP Professional
- Industry Leading Data Capabilities
- Powerful AI technology
- Patent DNA Extraction
Browse by: Latest US Patents, China's latest patents, Technical Efficacy Thesaurus, Application Domain, Technology Topic, Popular Technical Reports.
© 2024 PatSnap. All rights reserved.Legal|Privacy policy|Modern Slavery Act Transparency Statement|Sitemap|About US| Contact US: help@patsnap.com