Method for preparing rubber reinforcing filler by utilizing iron tailings
A technology for reinforcing fillers and iron tailings, which is applied in fibrous fillers, chemical instruments and methods, and inorganic pigment treatment. Comprehensive utilization value, the effect of small particle size
- Summary
- Abstract
- Description
- Claims
- Application Information
AI Technical Summary
Problems solved by technology
Method used
Examples
example 1
[0013] (1) Desliming of iron tailings in advance: the iron tailings are screened and washed several times through a cylindrical ore washing machine to remove sediment and grass roots in the iron tailings until they are clarified with water.
[0014] (2) Classification and regrinding of iron tailings: classify the iron tailings through a hydrocyclone, finely grind the sand through a Raymond mill, and then return to the hydrocyclone. The overflow particle size is controlled below 400 mesh.
[0015] (3) Preparation of high-purity quartz sand: the iron tailings are passed through a high-gradient magnetic separator with a magnetic strength of 15,000 Gauss to remove iron from the ultra-fine quartz sand, and then the quartz sand is placed in a temperature-controlled reactor, and oxalic acid is added , keep the temperature at 70°C, react for 25 hours, remove harmful trace metal and non-metal impurities in the ultrafine quartz powder, in the static workshop, use deionized water to wash ...
example 2
[0019] (1) Desliming of iron tailings in advance: the iron tailings are screened and washed several times through a cylindrical ore washing machine to remove sediment and grass roots in the iron tailings until they are clarified with water.
[0020] (2) Classification and regrinding of iron tailings: classify the iron tailings through a hydrocyclone, finely grind the sand through a Raymond mill, and then return to the hydrocyclone. The overflow particle size is controlled below 400 mesh.
[0021] (3) Preparation of high-purity quartz sand: iron tailings are removed from ultra-fine quartz sand through a high-gradient magnetic separator with a magnetic strength of 10,000 gauss, and then the quartz sand is placed in a temperature-controlled reactor and lemon is added. Acid and sodium petroleum sulfonate, constant temperature at 75°C, react for 30 hours, remove harmful trace metal and non-metallic impurities in ultrafine quartz powder, in the static workshop, use deionized water to...
example 3
[0025] (1) Desliming of iron tailings in advance: the iron tailings are screened and washed several times through a cylindrical ore washing machine to remove sediment and grass roots in the iron tailings until they are clarified with water.
[0026] (2) Classification and regrinding of iron tailings: classify the iron tailings through a hydrocyclone, finely grind the sand through a Raymond mill, and then return to the hydrocyclone. The overflow particle size is controlled below 400 mesh.
[0027] (3) Preparation of high-purity quartz sand: iron tailings are removed from the ultra-fine quartz sand by a high-gradient magnetic separator with a magnetic strength of 50 gauss, and then the quartz sand is placed in a temperature-controlled reactor, and lemon is added. Acid, constant temperature at 100°C, react for 25 hours, remove harmful trace metal and non-metal impurities in ultrafine quartz powder, in the static workshop, use deionized water to wash away harmful trace impurities o...
PUM
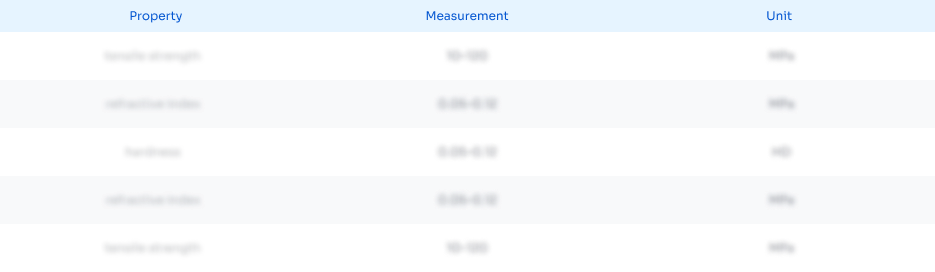
Abstract
Description
Claims
Application Information

- R&D
- Intellectual Property
- Life Sciences
- Materials
- Tech Scout
- Unparalleled Data Quality
- Higher Quality Content
- 60% Fewer Hallucinations
Browse by: Latest US Patents, China's latest patents, Technical Efficacy Thesaurus, Application Domain, Technology Topic, Popular Technical Reports.
© 2025 PatSnap. All rights reserved.Legal|Privacy policy|Modern Slavery Act Transparency Statement|Sitemap|About US| Contact US: help@patsnap.com