Ethylene propylene rubber insulation material for charging pile cables and preparation method of ethylene propylene rubber insulation material for charging pile cables
A technology of ethylene-propylene rubber insulation and EPDM rubber, which is applied in the direction of rubber insulators, insulated conductors, and insulated cables, can solve problems such as large load current value, aging, and heating of cable insulation materials, and achieve high insulation resistance and balance Good processing performance, high and low temperature resistance, and good insulation performance
- Summary
- Abstract
- Description
- Claims
- Application Information
AI Technical Summary
Problems solved by technology
Method used
Image
Examples
preparation example Construction
[0029] The above-mentioned preparation method of ethylene-propylene rubber insulating material for charging pile cables comprises the following steps:
[0030] (1) Add 100 parts of EPDM rubber to the internal mixer for internal mixing;
[0031] (2) Add 5-8 parts of zinc oxide, 1.2-2 parts of 2-mercaptobenzimidazole, 0.5-1 part of 2,2,4-trimethyl-1,2-dihydroquinoline polymer, four [β-(3,5-di-tert-butyl-4-hydroxyphenyl)propionic acid] 0.3-0.5 parts of pentaerythritol ester, 5-8 parts of microcrystalline wax, 8-12 parts of paraffin oil, 0.5-0.8 parts of stearic acid 1-2 parts of vinyl tris (b-methoxyethoxy) silane mixed in the internal mixer;
[0032] (3) 80-120 parts of surface-modified calcined clay, 30-50 parts of talcum powder, and continue mixing until the rubber is uniform;
[0033] (4) Unload the rubber material obtained in step (3) on the open mill, turn it over and cut it into rolls, and then put it into the rubber filter machine to filter the rubber. The filter screen...
Embodiment 1
[0038] 50 parts of EPDM 4725P, 50 parts of EPDM 4640, 3.0 parts of dicumyl peroxide, 1 part of triallyl isocyanurate, 5 parts of zinc oxide, calcined for surface modification 100 parts of pottery clay, 30 parts of talc powder, 1.5 parts of 2-mercaptobenzimidazole, 0.5 parts of 2,2,4-trimethyl-1,2-dihydroquinoline polymer, tetrakis[β-(3, 0.3 parts of 5-di-tert-butyl-4-hydroxyphenyl) propionate] pentaerythritol ester, 5 parts of microcrystalline wax, 12 parts of paraffin oil, 0.5 parts of stearic acid, vinyl tris(b-methoxyethoxy ) 1.2 parts of silane.
Embodiment 2
[0040] 40 parts of EPDM 4725P, 60 parts of EPDM 4640, 3.0 parts of dicumyl peroxide, 1 part of triallyl isocyanurate, 5 parts of zinc oxide, calcined for surface modification 100 parts of pottery clay, 30 parts of talc powder, 1.5 parts of 2-mercaptobenzimidazole, 0.5 parts of 2,2,4-trimethyl-1,2-dihydroquinoline polymer, tetrakis[β-(3, 0.3 parts of 5-di-tert-butyl-4-hydroxyphenyl) propionate] pentaerythritol ester, 5 parts of microcrystalline wax, 12 parts of paraffin oil, 0.5 parts of stearic acid, vinyl tris(b-methoxyethoxy ) 1.2 parts of silane.
PUM
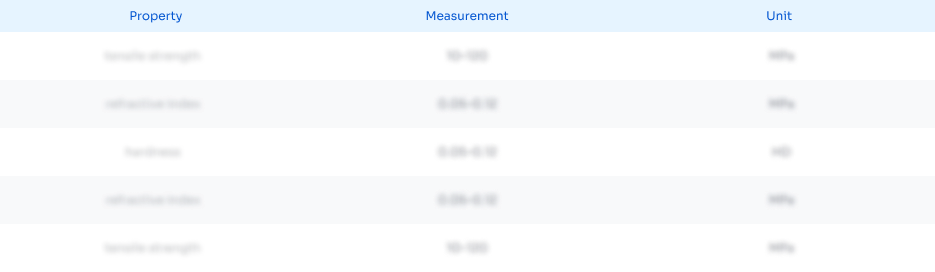
Abstract
Description
Claims
Application Information

- R&D
- Intellectual Property
- Life Sciences
- Materials
- Tech Scout
- Unparalleled Data Quality
- Higher Quality Content
- 60% Fewer Hallucinations
Browse by: Latest US Patents, China's latest patents, Technical Efficacy Thesaurus, Application Domain, Technology Topic, Popular Technical Reports.
© 2025 PatSnap. All rights reserved.Legal|Privacy policy|Modern Slavery Act Transparency Statement|Sitemap|About US| Contact US: help@patsnap.com