Dyeing and finishing processing method for real silk/cotton interweaved fabric
A processing method and fabric technology, applied in the direction of fabric surface trimming, textile material treatment, textile material continuous treatment, etc., can solve the problems of fabric gloss, fiber damage that cannot be repaired, silk fiber strong damage, etc., to achieve the size Good stability and pilling performance, guaranteed strong, strong damage effect
- Summary
- Abstract
- Description
- Claims
- Application Information
AI Technical Summary
Problems solved by technology
Method used
Examples
Embodiment 1
[0025] Specifications: 106.5 inches / JC80s*(JC80s+silk 100Nm) 100Nm / 200*160 satin.
[0026] The gray cloth goes through the following steps in turn:
[0027] 1. Turn the cloth, pad the amylase working solution 4g / L, adjust the pH to 7.0, and carry 120% of the liquid, roll it up and stack it at room temperature, wrap it with plastic film and rotate it at a constant speed for 6 hours, and wash it;
[0028] 2. Roll the fabric into the dyeing jigger, prepare the refining enzyme working solution, first adjust the pH value to 8.5 with soda ash, 2g / L of cellulose fiber refining enzyme, 2g / L of silk protein refining enzyme, temperature 50°C, and process with the jigger 2 hours, after the end, wash with high-temperature inactivated water, and then wash with water;
[0029] 3. Prepare the polishing enzyme working solution, adjust the pH value to 5.0 with an acid agent, add cellulose polishing enzyme 4g / L, the temperature is 60°C, and the time is 2 hours. After the end, wash with high-te...
Embodiment 2
[0035] Specifications: 106.5 inches / JC60s*(JC60s+silk 100Nm) / 200*100 satin.
[0036] The above-mentioned fabrics go through the following steps in turn:
[0037] 1. Turn the cloth, roll it into the dyeing jigger, adjust the pH of the working solution to 7.0, amylase 6g / L, temperature 60°C, treatment time 3 hours, wash with water;
[0038] 2. Roll the fabric into the jigger, prepare the refining enzyme working solution, first adjust the pH value to 8.0 with soda ash, 2g / L of cellulose fiber refining enzyme, 1.5g / L of silk protein refining enzyme, temperature 60°C, and the dyeing jigger Treat for 2 hours, wash with high-temperature inactivated water after the end, and then wash with clean water;
[0039] 3. Prepare the polishing enzyme working solution, adjust the pH value to 6.5 with an acid agent, add 10 g / L of cellulose polishing enzyme, temperature 60 ° C, time 3 hours, after the end, wash with high-temperature inactivated water, and then wash with water;
[0040] 4. Bleac...
Embodiment 3
[0045] Specifications: 106.5 inches / JC40s*(JC40s+silk 100Nm) / 144*96 satin.
[0046] The above-mentioned fabrics go through the following steps in turn:
[0047] 1. Turn the cloth, roll it into the jigger, adjust the pH of the working solution to 7.0, amylase 10g / L, temperature 60°C, treatment time 3 hours, wash with water;
[0048] 2. Roll the fabric into the dyeing jigger, prepare the refining enzyme working solution, first adjust the pH value to 9.0 with soda ash, 3g / L of cellulose fiber refining enzyme, 1.5g / L of silk protein refining enzyme, temperature 60°C, the dyeing jigger Treat for 2 hours, wash with high-temperature inactivated water after the end, and then wash with clean water;
[0049]3. Prepare the polishing enzyme working solution, adjust the pH value to 6.0 with an acid agent, add 5 g / L of cellulose polishing enzyme, temperature 60 ° C, time 3 hours, after the end, wash with high-temperature inactivated water, and then wash with water;
[0050] 4. Bleach hydr...
PUM
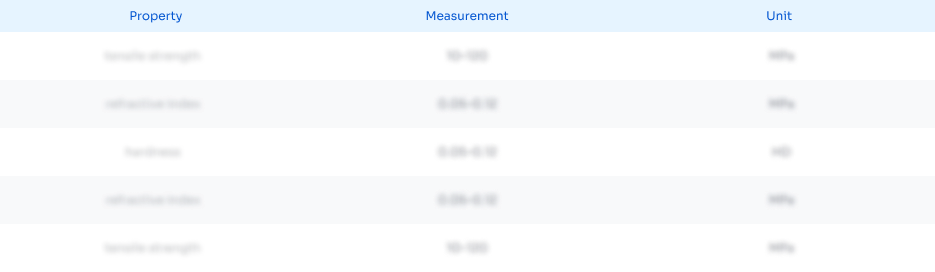
Abstract
Description
Claims
Application Information

- Generate Ideas
- Intellectual Property
- Life Sciences
- Materials
- Tech Scout
- Unparalleled Data Quality
- Higher Quality Content
- 60% Fewer Hallucinations
Browse by: Latest US Patents, China's latest patents, Technical Efficacy Thesaurus, Application Domain, Technology Topic, Popular Technical Reports.
© 2025 PatSnap. All rights reserved.Legal|Privacy policy|Modern Slavery Act Transparency Statement|Sitemap|About US| Contact US: help@patsnap.com