A kind of deep denitration combustion method of hedging boiler
A combustion method and boiler technology, applied in the combustion method, the use of multiple fuel combustion, combustion types, etc., can solve the problems of limited application scope, ammonia escape, and high boiler operating conditions, achieving wide applicability and reducing emissions. value, the effect of reducing the cost of denitration
- Summary
- Abstract
- Description
- Claims
- Application Information
AI Technical Summary
Problems solved by technology
Method used
Image
Examples
Embodiment 1
[0043] Such as figure 1 , figure 2 , image 3 , Figure 4 As shown, the hedging boiler has several layers of burn-off air nozzles 4 on the upper part of the front wall 7 and rear wall 8 of the furnace, and several layers of swirl burners on each layer of the lower part of the front wall 7 and rear wall 8 of the furnace. 1. The swirl burner 1 is provided with a primary air nozzle 2 and a secondary air nozzle 3, and the center line of the swirl burner 1 close to the two side walls 18 of each layer is offset to the center of the furnace by 5° to 45°, and the swirl flow The reducing air nozzle on the furnace wall between the burner 1 and the overfired air nozzle 4; Between the reduction zone 12 and the burnout zone 13 corresponding to the burnout air spout 4, purge air spouts 16 and 17 are set on both sides of the front and back walls of the furnace reduction zone 12 and the main combustion zone 14 near the two side walls 18 After the boiler air preheater, the tail flue passe...
Embodiment 2
[0047] Such as Figure 5 , Image 6 As shown, the difference between the present embodiment and the first embodiment is that an independent reduction inhibitor nozzle 19 is set in the primary air nozzle 2 of several swirl burners 1, and the end of the reduction inhibitor nozzle 19 is located at the primary air nozzle 2 Outside the end of the exhaust, the reduction inhibitor nozzle 19 is connected to the tail flue before the air preheater through the pipeline 10 and the fan 9, and the mixing pipe 15 is connected to the pipeline 10; during combustion, the tail smoke from the boiler air preheater The channel extracts part of the flue gas through the blower 9 as the transport medium of the amino reduction inhibitor, mixes it with the amino reduction inhibitor mixed through the dosing pipe 15, and sprays it into the furnace from the reduction inhibitor nozzle 19; this embodiment is more conducive to the realization of the furnace The reducing atmosphere and the temperature of the ...
Embodiment 3
[0049] Such as Figure 7 , Figure 8 As shown, the difference between the present embodiment and the second embodiment is only that several reduction inhibitor spouts 20 are relocated to the four corners of the hearth between the two-layer swirl burners 1 and on the front wall 7 and the rear wall 8; , the amino reduction inhibitor is injected into the amino reduction inhibitor through several reduction inhibitor spouts 20, and the amino reduction inhibitor of the same layer is sprayed in the manner of forming two imaginary tangential circles in the furnace; wherein the reduction inhibitor spout 20 aperture is 1~ 10mm, the opening is fan-shaped, the opening angle is between 10° and 150°, the injection speed of the amino reduction inhibitor is between 10m / s and 400m / s, and the diameter of the tangential circle can be adjusted by adjusting the deflection angle of the reduction inhibitor nozzle 20 The size and direction of rotation meet the needs of different working conditions; ...
PUM
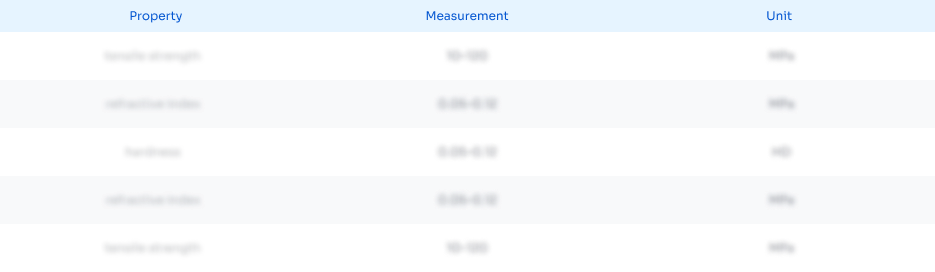
Abstract
Description
Claims
Application Information

- R&D Engineer
- R&D Manager
- IP Professional
- Industry Leading Data Capabilities
- Powerful AI technology
- Patent DNA Extraction
Browse by: Latest US Patents, China's latest patents, Technical Efficacy Thesaurus, Application Domain, Technology Topic, Popular Technical Reports.
© 2024 PatSnap. All rights reserved.Legal|Privacy policy|Modern Slavery Act Transparency Statement|Sitemap|About US| Contact US: help@patsnap.com