Natural-color liquid packaging paper and production process thereof
A packaging paper and liquid technology, applied in the field of papermaking, can solve the problems of affecting the uniformity of the surface layer slurry, affecting the covering property, etc., and achieve the effect of improving the surface covering property, reducing the gram weight, and reducing the requirements of forming and dehydration.
- Summary
- Abstract
- Description
- Claims
- Application Information
AI Technical Summary
Problems solved by technology
Method used
Image
Examples
Embodiment 1
[0037] A kind of natural color liquid wrapping paper, it comprises following production steps:
[0038] 1. Pulping steps
[0039] a. The pulping process of the surface paper layer: After the pulp board is disintegrated by a hydropulper according to a certain ratio, it is screened, beaten, and pulped, and finally the paper feeder is sent for copying, wherein, by weight percentage, the surface paper The pulp composition of the paper layer is: 40% bleached hardwood kraft pulp, 60% bleached softwood kraft pulp.
[0040] b. The pulping process of the backing paper layer: After the pulp board is disintegrated by a hydropulper according to a certain ratio, it is screened, beaten, and pulped, and finally the paper feeder enters the paper making process, wherein, in terms of weight percentage, the surface The pulp composition of the paper layer is: 40% bleached hardwood kraft pulp, 60% bleached softwood kraft pulp.
[0041] c. The pulping process of the core paper layer: After the pu...
Embodiment 2
[0055] The production process of the natural color liquid wrapping paper of the present embodiment is similar to embodiment 1, and difference is:
[0056] In this embodiment, by weight percentage, the slurry composition of the face paper layer is: 30% bleached hardwood kraft pulp, 70% bleached softwood kraft pulp; the slurry composition of the backing paper layer is : 70% bleached hardwood kraft pulp, 30% bleached softwood kraft pulp; the pulp composition of the core paper layer is: 10% chemithermomechanical pulp, 80% unbleached virgin wood pulp, 10% broken paper ; The slurry composition of the bottom paper layer is 100% unbleached virgin wood pulp.
[0057] In the wet end chemical step of this embodiment, based on the weight of each layer of slurry, the amount of aluminum sulfate added is: face paper layer 30kg / t, backing paper layer 15kg / t, core paper layer 6kg / t, bottom paper Layer 16kg / t; the amount of cationic rosin added is: face paper layer 50kg / t, backing paper layer ...
Embodiment 3
[0063] The production process of the natural color liquid wrapping paper of the present embodiment is similar to embodiment 1, and difference is:
[0064] In this embodiment, by weight percentage, the slurry composition of the face paper layer is: 70% bleached hardwood kraft pulp, 30% bleached softwood kraft pulp; the slurry composition of the lining paper layer is: : 30% bleached hardwood kraft pulp, 70% bleached softwood kraft pulp; the pulp composition of the core paper layer is: 40% chemical thermomechanical pulp, 30% unbleached virgin wood pulp, 30% broken paper ; The slurry composition of the bottom paper layer is 100% unbleached virgin wood pulp.
[0065]In the wet end chemical step of this embodiment, based on the weight of each layer of slurry, the amount of aluminum sulfate added is: face paper layer 15kg / t, backing paper layer 30kg / t, core paper layer 30kg / t, bottom paper Layer 30kg / t; the amount of cationic rosin added is: face paper layer 5kg / t, backing paper lay...
PUM
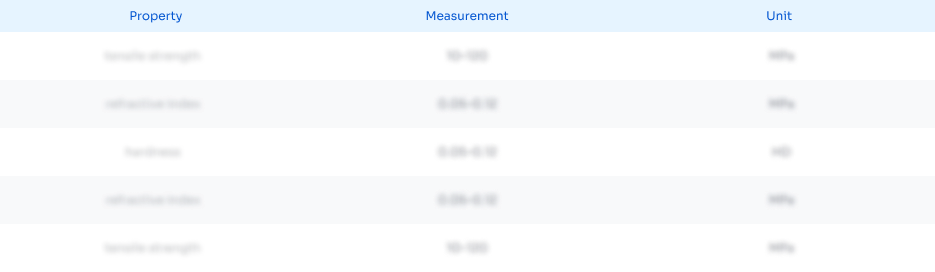
Abstract
Description
Claims
Application Information

- Generate Ideas
- Intellectual Property
- Life Sciences
- Materials
- Tech Scout
- Unparalleled Data Quality
- Higher Quality Content
- 60% Fewer Hallucinations
Browse by: Latest US Patents, China's latest patents, Technical Efficacy Thesaurus, Application Domain, Technology Topic, Popular Technical Reports.
© 2025 PatSnap. All rights reserved.Legal|Privacy policy|Modern Slavery Act Transparency Statement|Sitemap|About US| Contact US: help@patsnap.com