Method for extracting vanadium from vanadium-containing solution
A solution and extraction technology, which is applied in the field of vanadium extraction, can solve the problems of reduced unit emulsion processing capacity, lower production efficiency, and large amount of extractant, and achieve the effects of less amount of extractant, high production efficiency, and strong continuous productivity
- Summary
- Abstract
- Description
- Claims
- Application Information
AI Technical Summary
Problems solved by technology
Method used
Examples
Embodiment 1
[0031] A method for extracting vanadium from a solution containing vanadium. The concrete steps of described method are:
[0032] Step 1. Prepare and mix the organic phase
[0033] Mix 5-9% of carrier, 8-9% of liquid paraffin, 2-5% of surfactant and the rest as film solvent to obtain a mixed organic phase according to volume percentage.
[0034] Step 2. Prepare the emulsion
[0035] Then mix the organic phase according to the description: the volume ratio of the stripping agent is 1: (1 ~ 1.1), add the stripping agent to the mixing organic phase, and make it under the condition that the rotation speed is 2000 ~ 3000r / min Stir for 5 to 20 minutes to obtain an emulsion.
[0036] The concentration of the stripping agent is 0.2-1mol / L.
[0037] Step 3, liquid film extraction
[0038] According to the volume ratio of the emulsion: the vanadium-containing solution is 1: (2 ~ 5), the emulsion and the vanadium-containing solution are mixed, stirred for 10 ~ 30min, left to stand, ...
Embodiment 2
[0046] A method for extracting vanadium from a solution containing vanadium. Except following components all the other are with embodiment 1:
[0047] The carrier is a mixture of an alkaline extractant and a neutral extractant; the surfactant is a polyamine surfactant; the membrane solvent is a mixture of alcohols and ketone organic solvents; the stripping agent is sodium carbonate solution.
Embodiment 3
[0049] A method for extracting vanadium from a solution containing vanadium. The concrete steps of described method are:
[0050] Step 1. Prepare and mix the organic phase
[0051] Mix 7-11% of carrier, 9-10% of liquid paraffin, 3-6% of surfactant and the rest as film solvent to obtain a mixed organic phase.
[0052] Step 2. Prepare the emulsion
[0053] Then mix the organic phase according to the description: the volume ratio of the stripping agent is 1: (1.1 ~ 1.2), add the stripping agent in the mixing organic phase, and stir under the condition of 2000 ~ 3000r / min at a rotating speed 5~20min, the emulsion is obtained.
[0054] The concentration of the stripping agent is 0.6-1.4mol / L.
[0055] Step 3, liquid film extraction
[0056] According to the volume ratio of the emulsion: the vanadium-containing solution is 1: (3 ~ 6), the emulsion and the vanadium-containing solution are mixed, stirred for 20 ~ 40min, left to stand, and phase-separated to obtain a loaded vanadi...
PUM
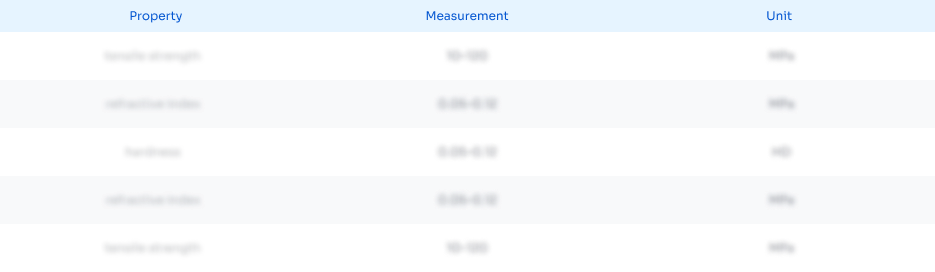
Abstract
Description
Claims
Application Information

- R&D Engineer
- R&D Manager
- IP Professional
- Industry Leading Data Capabilities
- Powerful AI technology
- Patent DNA Extraction
Browse by: Latest US Patents, China's latest patents, Technical Efficacy Thesaurus, Application Domain, Technology Topic, Popular Technical Reports.
© 2024 PatSnap. All rights reserved.Legal|Privacy policy|Modern Slavery Act Transparency Statement|Sitemap|About US| Contact US: help@patsnap.com