Multiphysics Numerical Calculation Method of Thermal Flow Microstructure in Friction Welding Process
A technology of microstructure and numerical calculation, applied in the direction of calculation, manufacturing calculation system, computer aided design, etc., can solve the problems of low matching degree, low efficiency and precision of friction welding process
- Summary
- Abstract
- Description
- Claims
- Application Information
AI Technical Summary
Problems solved by technology
Method used
Image
Examples
Embodiment
[0049] like figure 1 As shown, the multi-physics numerical calculation method of the thermal flow microstructure of the friction welding process includes the following steps in sequence: Step 1, establishing a heat-fluid coupling numerical model; Step 2, performing a fully coupled calculation of temperature and flow field, and obtaining The size and distribution of the temperature and flow field at any time in the process; step 3, calculate the microstructure transformation, and obtain the distribution of the phase transition structure; step 4, establish a heat-force-flow-structure coupling numerical model; step 5, calculate the plasticity of the workpiece during the welding process Area and stress-strain.
[0050] The Johndon-Cook model is used to describe the friction welding material when the heat-flow fully coupled numerical model and the heat-force-flow-structure coupled numerical model of this embodiment are established. The expression of the Johndon-Cook model is:
[0...
PUM
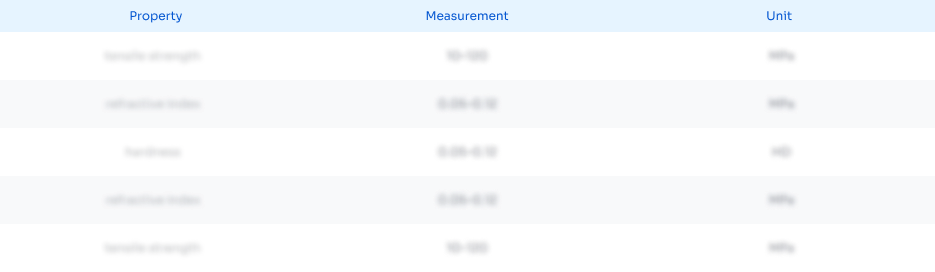
Abstract
Description
Claims
Application Information

- R&D
- Intellectual Property
- Life Sciences
- Materials
- Tech Scout
- Unparalleled Data Quality
- Higher Quality Content
- 60% Fewer Hallucinations
Browse by: Latest US Patents, China's latest patents, Technical Efficacy Thesaurus, Application Domain, Technology Topic, Popular Technical Reports.
© 2025 PatSnap. All rights reserved.Legal|Privacy policy|Modern Slavery Act Transparency Statement|Sitemap|About US| Contact US: help@patsnap.com