A high temperature and corrosion resistant glass coating for aluminum liquid stirring
A high-temperature and corrosion-resistant glass coating technology, applied in anti-corrosion coatings, fire-resistant coatings, coatings, etc., can solve the problems of shortening the service life of stirring tools, easy pollution of aluminum liquid, serious corrosion, etc., and achieves high density and aluminum resistance. Good liquid corrosion and the effect of promoting densification
- Summary
- Abstract
- Description
- Claims
- Application Information
AI Technical Summary
Problems solved by technology
Method used
Image
Examples
Embodiment 1
[0044] Weigh a certain amount of A-component glass, B-component glass, vermiculite, polyacrylate and silicone resin according to the ratio in Table 1, and perform the ratio, stirring, surface cleaning, coating, and drying in sequence according to the aforementioned steps and other procedures, the dried samples were placed in a program-controlled furnace for sintering, and the sintering conditions were 550°C and 750°C for 2 hours respectively; among them, the raw materials of component A glass were: 20% strontium carbonate, 30% calcium carbonate, 30% silicon dioxide, 15% boric acid, 5% titanium dioxide, the raw materials of component B glass are: 5% aluminum oxide, 35% boric acid, 15% sodium carbonate, 40% zinc oxide, and 5% silicon dioxide.
Embodiment 2
[0046] Weigh a certain amount of A-component glass, B-component glass, vermiculite, polyacrylate and silicone resin according to the ratio in Table 1, and perform the ratio, stirring, surface cleaning, coating, and drying in sequence according to the aforementioned steps and other procedures, the dried samples are placed in a program-controlled furnace for sintering, and the sintering conditions are 600°C and 760°C for 1.5h respectively; among them, the raw materials of component A glass are: 30% strontium carbonate, 20% calcium carbonate , 36% silicon dioxide, 10% boric acid, 4% titanium dioxide, the raw materials of component B glass are: 10% alumina, 50% boric acid, 5% sodium carbonate, 25% zinc oxide, 10% silicon dioxide.
Embodiment 3
[0048] Weigh a certain amount of A-component glass, B-component glass, vermiculite, polyacrylate and silicone resin according to the ratio in Table 1, and perform the ratio, stirring, surface cleaning, coating, and drying in sequence according to the aforementioned steps and other processes, the dried samples were placed in a program-controlled furnace for sintering, and the sintering conditions were 650°C and 780°C for 1 hour respectively; among them, the raw materials of component A glass were: 25% strontium carbonate, 25% calcium carbonate, Silicon dioxide 37%, boric acid 5%, titanium dioxide 8%, the raw materials of component B glass are: aluminum oxide 10%, boric acid 50%, sodium carbonate 8%, zinc oxide 30%, silicon dioxide 2%.
PUM
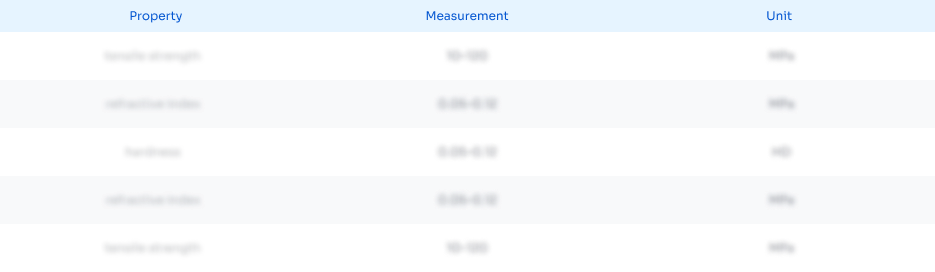
Abstract
Description
Claims
Application Information

- R&D
- Intellectual Property
- Life Sciences
- Materials
- Tech Scout
- Unparalleled Data Quality
- Higher Quality Content
- 60% Fewer Hallucinations
Browse by: Latest US Patents, China's latest patents, Technical Efficacy Thesaurus, Application Domain, Technology Topic, Popular Technical Reports.
© 2025 PatSnap. All rights reserved.Legal|Privacy policy|Modern Slavery Act Transparency Statement|Sitemap|About US| Contact US: help@patsnap.com