Plastic thin film and preparation method thereof
A plastic film and raw material technology, applied in the field of plastic film and its preparation, can solve the problems of difficult to meet the requirements of industrial production, poor tensile strength of plastic film, etc., to meet the needs of daily life and industrial production, good water resistance, preparation The effect of simple process
- Summary
- Abstract
- Description
- Claims
- Application Information
AI Technical Summary
Problems solved by technology
Method used
Examples
Embodiment 1
[0017] A plastic film, which is made of the following raw materials in parts by weight: 42 parts of polyvinyl chloride, 45 parts of polypropylene resin, 9 parts of polyethylene wax, 12 parts of talcum powder, 7 parts of organic montmorillonite, polyvinyl alcohol 48 parts, 10 parts of sodium titanium phosphate, 22 parts of polyacryloyl, 1.6 parts of dicumyl peroxide, 1.4 parts of antioxidant, 11 parts of calcium carbonate, 0.45 parts of silane coupling agent, 9 parts of dioctyl phthalate , 1.3 parts of light stabilizer, 5.6 parts of glyceryl tristearate, 3.7 parts of styrene-acrylonitrile copolymer, 1 part of plasticizer.
[0018] The preparation method of described plastic film, comprises the following steps:
[0019] (1) Take each raw material component according to the ratio in parts by weight;
[0020] (2) adding each raw material component prepared in the step (1) into the kneader and fully stirring and uniformly mixing to obtain a raw material mixture;
[0021] (3) Add ...
Embodiment 2
[0023] A plastic film, which is made of the following raw materials in parts by weight: 52 parts of polyvinyl chloride, 45 parts of polypropylene resin, 9 parts of polyethylene wax, 12 parts of talcum powder, 7 parts of organic montmorillonite, polyvinyl alcohol 42 parts, 10 parts of sodium titanium phosphate, 18 parts of polyacryloyl, 2.2 parts of dicumyl peroxide, 1.2 parts of antioxidant, 9 parts of calcium carbonate, 0.5 parts of silane coupling agent, 9 parts of dioctyl phthalate , 1 part of light stabilizer, 4 parts of glyceryl tristearate, 2.5 parts of styrene-acrylonitrile copolymer, 1.2 parts of plasticizer.
[0024] The preparation method of described plastic film, comprises the following steps:
[0025] (1) Take each raw material component according to the ratio in parts by weight;
[0026] (2) adding each raw material component prepared in the step (1) into the kneader and fully stirring and uniformly mixing to obtain a raw material mixture;
[0027] (3) Add the ...
Embodiment 3
[0029] A plastic film, which is made of the following raw materials in parts by weight: 45 parts of polyvinyl chloride, 54 parts of polypropylene resin, 11 parts of polyethylene wax, 10 parts of talcum powder, 6 parts of organic montmorillonite, polyvinyl alcohol 38 parts, 10 parts of sodium titanium phosphate, 20 parts of polyacryloyl, 3 parts of dicumyl peroxide, 2 parts of antioxidant, 10 parts of calcium carbonate, 0.5 parts of silane coupling agent, 10 parts of dioctyl phthalate , 1.6 parts of light stabilizer, 4.8 parts of glyceryl tristearate, 2.6 parts of styrene-acrylonitrile copolymer, 1 part of plasticizer.
[0030] The preparation method of described plastic film, comprises the following steps:
[0031] (1) Take each raw material component according to the ratio in parts by weight;
[0032] (2) adding each raw material component prepared in the step (1) into the kneader and fully stirring and uniformly mixing to obtain a raw material mixture;
[0033] (3) Add the...
PUM
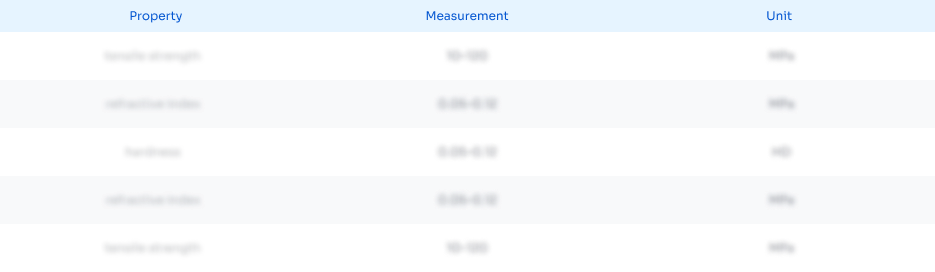
Abstract
Description
Claims
Application Information

- R&D
- Intellectual Property
- Life Sciences
- Materials
- Tech Scout
- Unparalleled Data Quality
- Higher Quality Content
- 60% Fewer Hallucinations
Browse by: Latest US Patents, China's latest patents, Technical Efficacy Thesaurus, Application Domain, Technology Topic, Popular Technical Reports.
© 2025 PatSnap. All rights reserved.Legal|Privacy policy|Modern Slavery Act Transparency Statement|Sitemap|About US| Contact US: help@patsnap.com