Correction processing method of fixture wheel groove profile for static-frequency detection
A processing method and a wheel groove technology are applied in the field of correction and processing of the wheel groove profile of a fixture for static frequency detection, which can solve the problem of scrapping wheel groove blocks for frequency measurement, poor visual processing surface waviness, easy to produce scratches, pulling marks, etc.
- Summary
- Abstract
- Description
- Claims
- Application Information
AI Technical Summary
Problems solved by technology
Method used
Image
Examples
Embodiment Construction
[0011] The invention discloses a method for correcting the wheel groove profile of a fixture for static frequency detection, which includes sequentially performing fine milling and correcting processing, wherein the fine milling process uses a fine milling forming knife 1 to process the designed blade root wheel groove profile Outlet root groove profile A, see figure 1 , figure 1 The dotted line in the figure shows the outline of the finish milling cutter 1; the correction process uses the same finish milling cutter as the finish milling process, on the basis of the blade root wheel groove profile A, and then proceeds to the position of the correction height h as a whole. In one finish milling process, since the correction process only processes the inner back working surface of the root wheel groove, and the non-working surface of the blade root wheel groove does not participate in cutting, the profile line A1 of the non-working surface of the blade root wheel groove obtained...
PUM
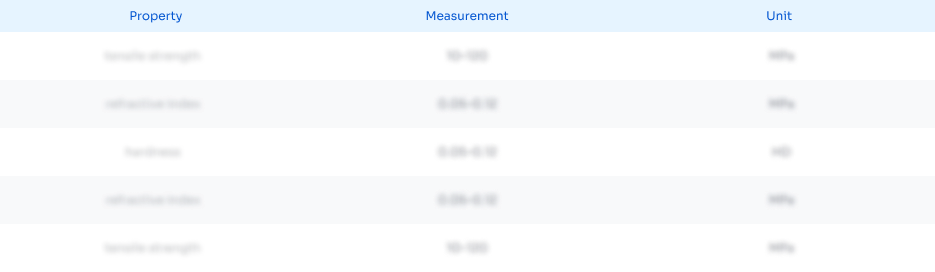
Abstract
Description
Claims
Application Information

- Generate Ideas
- Intellectual Property
- Life Sciences
- Materials
- Tech Scout
- Unparalleled Data Quality
- Higher Quality Content
- 60% Fewer Hallucinations
Browse by: Latest US Patents, China's latest patents, Technical Efficacy Thesaurus, Application Domain, Technology Topic, Popular Technical Reports.
© 2025 PatSnap. All rights reserved.Legal|Privacy policy|Modern Slavery Act Transparency Statement|Sitemap|About US| Contact US: help@patsnap.com