Tempering technology for NdFeB magnet
A NdFeB, magnet technology, applied in magnetic objects, magnetic materials, inductance/transformer/magnet manufacturing and other directions, can solve the problems that the magnetic performance cannot be maximized and cannot meet the requirements.
- Summary
- Abstract
- Description
- Claims
- Application Information
AI Technical Summary
Problems solved by technology
Method used
Image
Examples
Embodiment 1
[0077] The composition of a alloy is: Pr-Nd: 29.5%; Dy: 0.9%; Nb: 0.25%; Al: 0.3%; B: 1.01%; Cu: 0.15%; Co: 1%; Ho: 0.6%; the balance For Fe.
[0078] The sintered a-alloy prepared by the traditional sintered NdFeB process is subjected to primary tempering, that is, evacuated to below 1Pa, heated to 900°C for 4 hours, and cooled to 80°C with argon air; Fire, that is, evacuate to below 1Pa, heat to 515°C, cool down to 500°C after 2 hours, and cool at 500°C for 2 hours, take the sample after secondary tempering as a1 and test the density and magnetic properties; finally carry out Three-stage tempering, that is, evacuate to below 1Pa, heat to 475°C, cool down to 460°C after 2 hours, and cool at 460°C for 2 hours, take the sample after the three-stage tempering as a2 and test the density and magnetic properties .
Embodiment 2
[0080] The composition of the alloy is Pr-Nd: 29%; Dy: 0.8%; Tb: 0.5%; Nb: 0.25%; Al: 0.3%; B: 1.01%; Cu: 0.25%; Co: 1%; Ho: 0.5% ; The balance is Fe.
[0081] The sintered b-alloy prepared by the traditional sintered NdFeB process is subjected to primary tempering, that is, evacuated to below 1Pa, heated to 900°C and kept for 4 hours, then air-cooled to 80°C with argon air to be released; and then subjected to secondary tempering Fire, that is, evacuate to below 1Pa, heat to 530°C, cool down to 515°C after 2 hours, and cool at 515°C for 2 hours, take the sample after secondary tempering as b1 and test the density and magnetic properties; Three-stage tempering, that is, evacuate to below 1Pa, heat to 490°C, cool down to 475°C after 2 hours, and cool at 475°C for 2 hours, take the sample after the three-stage tempering as b2 and test the density and magnetic properties ;Finally, perform four-stage tempering, that is, vacuumize to below 1Pa, heat to 475°C, cool down to 460°C af...
PUM
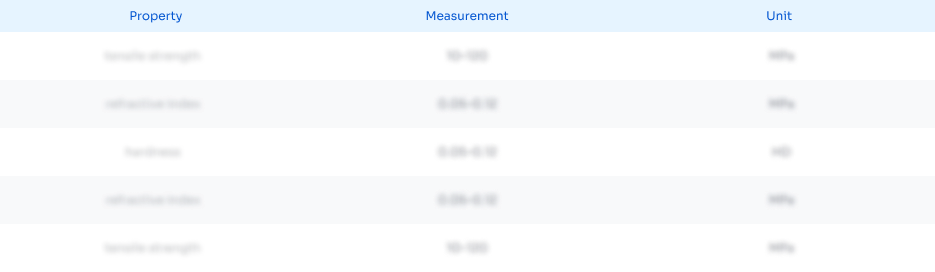
Abstract
Description
Claims
Application Information

- R&D Engineer
- R&D Manager
- IP Professional
- Industry Leading Data Capabilities
- Powerful AI technology
- Patent DNA Extraction
Browse by: Latest US Patents, China's latest patents, Technical Efficacy Thesaurus, Application Domain, Technology Topic, Popular Technical Reports.
© 2024 PatSnap. All rights reserved.Legal|Privacy policy|Modern Slavery Act Transparency Statement|Sitemap|About US| Contact US: help@patsnap.com