Process method for recovering rare earth from cerium oxide waste material
A process method, cerium oxide technology, applied in the field of hydrometallurgy, to achieve the effect of simple and feasible process method, high rare earth recovery rate, and easy large-scale use
- Summary
- Abstract
- Description
- Claims
- Application Information
AI Technical Summary
Problems solved by technology
Method used
Examples
Embodiment 1
[0012] Take 30g of cerium oxide waste (REO 82.03wt%) through a 100-mesh sieve to remove solid impurities such as weeds and gravel, then add 1.2 times the theoretical amount of sulfuric acid and 1.2 times the theoretical amount of FeSO 4 , heated to 45°C-55°C under constant stirring for 1.5h, and solid-liquid separation was carried out to obtain a primary leachate, the primary leachate was neutralized with MgO to remove impurities, and the second solid-liquid separation was obtained to obtain a secondary leachate, in the leachate The recovery rate of rare earth elements is 83.23%.
Embodiment 2
[0014] Take 30g of cerium oxide waste (REO 82.03wt%) and pass through a 100-mesh sieve to remove solid impurities such as weeds and gravel, then add 1.3 times the theoretical amount of sulfuric acid and 1.3 times the theoretical amount of FeSO 4 , heated to 45°C-55°C under constant stirring for 1h, and solid-liquid separation was carried out to obtain a primary leachate, the primary leachate was neutralized with MgO to remove impurities, and then the second solid-liquid separation was obtained to obtain a secondary leachate, the leachate The recovery rate of rare earth elements was 81.58%.
Embodiment 3
[0016] Take 30g of cerium oxide waste (REO 82.03wt%) through a 100-mesh sieve to remove solid impurities such as weeds and gravel, then add 1.4 times the theoretical amount of sulfuric acid and 1.4 times the theoretical amount of FeSO 4 , heated to 45°C-55°C under constant stirring for 1h, and solid-liquid separation was carried out to obtain a primary leachate, the primary leachate was neutralized with MgO to remove impurities, and then the second solid-liquid separation was obtained to obtain a secondary leachate, the leachate The recovery rate of rare earth elements was 82.11%.
PUM
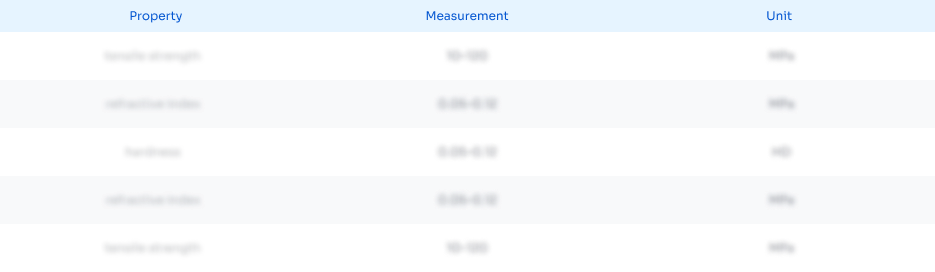
Abstract
Description
Claims
Application Information

- Generate Ideas
- Intellectual Property
- Life Sciences
- Materials
- Tech Scout
- Unparalleled Data Quality
- Higher Quality Content
- 60% Fewer Hallucinations
Browse by: Latest US Patents, China's latest patents, Technical Efficacy Thesaurus, Application Domain, Technology Topic, Popular Technical Reports.
© 2025 PatSnap. All rights reserved.Legal|Privacy policy|Modern Slavery Act Transparency Statement|Sitemap|About US| Contact US: help@patsnap.com