Catalyst for decomposing hydrogen peroxide and method for decomposing hydrogen peroxide in epoxidation reaction product
A technology of epoxidation reaction and hydrogen peroxide, applied in metal/metal oxide/metal hydroxide catalyst, physical/chemical process catalyst, chemical instrument and method, etc. report and other issues to achieve the effect of eliminating potential hazards and improving safety
- Summary
- Abstract
- Description
- Claims
- Application Information
AI Technical Summary
Problems solved by technology
Method used
Examples
preparation example Construction
[0018] According to the method of the present invention, wherein, the preparation method of described hydrogen peroxide decomposition catalyst comprises: 1) with IIIA group metal hydroxide or oxide compound, VB group metal salt or oxide compound, acidic aluminum sol, organic extrusion aid , organic porogen and paste-forming agent are fully kneaded to obtain a wet plastomer, and then the wet plastomer is extruded into a wet strip; 2) the wet strip obtained in step 1) is dried and roasted , to obtain a metal oxide catalyst comprising a metal oxide of group VB and a metal oxide of group IIIA; 3) impregnating the metal oxide catalyst obtained in step 2) with a group IB metal salt solution and a rare earth metal salt solution, and then drying and roasting, A composite metal oxide catalyst comprising VB group metal oxides, IB group metal oxides, rare earth metal oxides and IIIA group metal oxides is obtained.
[0019] In the preparation method, the VB metal salt or oxide is a metal ...
Embodiment 1
[0043] With 317.82 grams of aluminum hydroxide powder (72.2 mass % of aluminum oxide content, produced by Shandong Zibo Taiguang Chemical Co., Ltd.), 16.85 grams of ammonium metavanadate (analytical reagent), 7.50 grams of Sesame powder (produced by Henan Lankao Vegetable Gum Factory) , 378.72 grams of aluminum oxide content is 22.4 mass % aluminum sol (Hunan Jianchang Petrochemical Co., Ltd. production), 15.00 grams of octylphenol polyoxyethylene (15) ether (OP-15, Hebei Xingtai Kewang Chemical Auxiliary Co., Ltd. Produced by the company) and 60.36 grams of deionized water are fully kneaded in a multifunctional catalyst molding machine (produced by the General Factory of Science and Technology Industry of South China University of Technology) to obtain a wet plastic body, and then extruded into a solid cylindrical strip of φ1.2mm. After drying at ~30°C for 21 hours, put it into a drying oven and dry at 50°C for 4 hours, then put it into a box-type resistance furnace, heat it f...
Embodiment 2
[0049] Adopt and embodiment 1 same method to prepare composite metal oxide catalyst and carry out the catalytic decomposition of hydrogen peroxide, difference is: have 50.00 gram aqueous solution that is dissolved with 6.376 gram copper nitrate trihydrate and 5.714 gram lanthanum nitrate hexahydrate at 25 Impregnate 30.00 g of cylindrical bar catalysts containing 3.96% by mass of vanadium pentoxide and 96.04% by mass of aluminum oxide at ~30°C for 36 hours, then dry the impregnated matter at 105°C for 12 hours, and then dry the dry matter at 650°C Roasting 20 hours, after natural cooling, obtain the cylindrical bar composite metal oxide catalyst that comprises 3.47 mass % vanadium pentoxide, 6.13 mass % copper oxide, 6.28 mass % lanthanum trioxide and 84.12 mass % aluminum oxide, the hydrogen peroxide of catalyzer The decomposition results are shown in Table 2.
[0050] Table 2
[0051] Reaction time / h
PUM
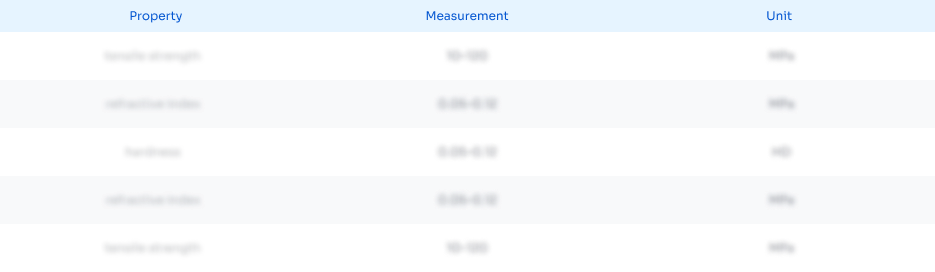
Abstract
Description
Claims
Application Information

- Generate Ideas
- Intellectual Property
- Life Sciences
- Materials
- Tech Scout
- Unparalleled Data Quality
- Higher Quality Content
- 60% Fewer Hallucinations
Browse by: Latest US Patents, China's latest patents, Technical Efficacy Thesaurus, Application Domain, Technology Topic, Popular Technical Reports.
© 2025 PatSnap. All rights reserved.Legal|Privacy policy|Modern Slavery Act Transparency Statement|Sitemap|About US| Contact US: help@patsnap.com