A kind of preparation technology of ceramic cover plate
A preparation process and a technology for a ceramic cover, which are applied in the field of preparation technology of a ceramic cover plate of microwave packaging, can solve the problems of low dimensional accuracy of finished products, deformation, easy cracking yield, etc., so as to improve the yield and product accuracy, and improve sealing performance Effect
- Summary
- Abstract
- Description
- Claims
- Application Information
AI Technical Summary
Problems solved by technology
Method used
Image
Examples
Embodiment 1
[0051] 1. Weighing: The solid raw material is 92% alumina, 3% calcium oxide, 2% magnesium oxide, 2% silicon dioxide, 0.5% nickel, 0.2% La 2 o 3 and 0.3% are weighed respectively by proportioning;
[0052] 2. Ball milling: Mix the solid raw materials evenly before ball milling to ensure that the mesh size of the mixed powder after ball milling is within the range of 3000-4000 mesh;
[0053] 3. Mixing: mix the mixed powder after ball milling with the organic solvent in a ratio of 1:1 by weight to form a slurry; wherein, the organic solvent is ethanol: methyl ethyl ketone = 1:1.5.
[0054] 4. Molding: According to the product requirements, make a ceramic cover plate mold and a ceramic base mold, inject the slurry pressurized to 0.3MPa into the ceramic cover plate mold and the ceramic base mold respectively, and obtain a ceramic cover plate blank and a ceramic base body;
[0055] 5. Assembly: After covering the ceramic base body with a layer of 0.5mm thick adhesive powder, the...
Embodiment 2
[0060] 1. Weighing: The solid raw material is 88% alumina, 3% calcium oxide, 4% magnesium oxide, 3% silicon dioxide, 0.3% molybdenum, 0.7% iron and 1% Ce 2 o 3 Weigh separately according to the proportion;
[0061] 2. Ball milling: Mix the solid raw materials evenly before ball milling to ensure that the mesh size of the mixed powder after ball milling is within the range of 2000-4000 mesh;
[0062] 3. Mixing: mix the mixed powder after ball milling with organic solvent in a ratio of 1:1.5 by weight to form a slurry; wherein, the organic solvent is ethanol:trichloroethylene=1:2.
[0063] 4. Molding: According to the product requirements, make a ceramic cover mold and a ceramic base mold, inject the slurry pressurized to 0.4MPa into the ceramic cover mold and the ceramic base mold respectively, and obtain a ceramic cover plate body and a ceramic base body;
[0064] 5. Assembly: After covering the ceramic base body with a layer of 0.3mm thick adhesive powder, then assemble th...
Embodiment 3
[0069] 1. Weighing: the solid raw material is 90% alumina, 5% calcium oxide, 3% magnesium oxide, 1% silicon dioxide, 0.2% titanium, 0.5% ZrO 2 and 0.3%CeO 2 Rare earth metal oxides are weighed respectively according to the proportioning ratio;
[0070] 2. Ball milling: After mixing the solid raw materials evenly, carry out ball milling to ensure that the mesh number of the mixed powder after ball milling is within the range of 2000-2500 mesh;
[0071] 3. Mixing: mix the mixed powder after ball milling with organic solvent in a weight ratio of 1:2 to form a slurry; among them, the organic solvent is ethanol:toluene=1:1.
[0072] 4. Molding: According to the product requirements, make a ceramic cover mold and a ceramic base mold, inject the slurry pressurized to 0.5MPa into the ceramic cover mold and the ceramic base mold respectively, and obtain a ceramic cover plate body and a ceramic base body;
[0073] 5. Assembly: After covering the ceramic base body with a layer of 0.6m...
PUM
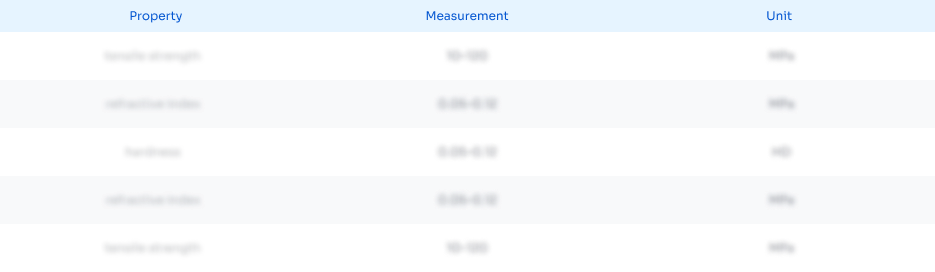
Abstract
Description
Claims
Application Information

- R&D
- Intellectual Property
- Life Sciences
- Materials
- Tech Scout
- Unparalleled Data Quality
- Higher Quality Content
- 60% Fewer Hallucinations
Browse by: Latest US Patents, China's latest patents, Technical Efficacy Thesaurus, Application Domain, Technology Topic, Popular Technical Reports.
© 2025 PatSnap. All rights reserved.Legal|Privacy policy|Modern Slavery Act Transparency Statement|Sitemap|About US| Contact US: help@patsnap.com