Novel foaming material
A foaming material, a new technology, applied in the field of new foaming materials, can solve the problems of poor impact resistance, poor durability, etc., and achieve good wind pressure resistance, excellent thermal insulation, and high compressive strength.
- Summary
- Abstract
- Description
- Claims
- Application Information
AI Technical Summary
Problems solved by technology
Method used
Image
Examples
preparation example Construction
[0030] The preparation method of the environmental protection brick comprises the following steps:
[0031] S1: Preparation of hollow bricks
[0032] Mix cement, shale ore, fly ash, tailings sand, and kaolin, and stir evenly at a speed of 200-400r / min to make hollow bricks;
[0033] S2: Preparation of new foam materials
[0034] S21: Stir cement, glyoxal and water evenly at a speed of 100-300r / min to prepare a slurry;
[0035] S22: Calcium silicate, calcium sulfate, bentonite, magnesium borate, corn stalk powder, AR glass fiber, carbon fiber, water reducer, foaming agent, foam regulator, catalyst, crosslinking agent and foam stabilizer Stir for 2-3 hours at a rotational speed of 60-100r / min to obtain a foam solution;
[0036] S23: Add the foam liquid prepared in step S22 to the slurry prepared in step S21, and stir evenly at a rotating speed of 150-200r / min to prepare a new foam material;
[0037] S3: Preparation of insulation bricks
[0038] Fill the cavity of the hollow...
Embodiment 1
[0041] An environmentally friendly brick, comprising a hollow brick as a brick body shell and a new type of foam material filled in the cavity of the brick body, the hollow brick includes the following raw materials in parts by weight: 55 parts of cement, 40 parts of shale ore, powder 30 parts of coal ash, 12 parts of tailings sand, and 9 parts of kaolin; the new foaming material is in parts by weight, including the following raw materials: 35 parts of cement, 3 parts of calcium silicate, 2 parts of calcium sulfate, and 2 parts of bentonite , 2 parts of magnesium borate, 1.8 parts of corn straw powder, 0.9 parts of AR glass fiber, 0.5 parts of carbon fiber, 2 parts of water reducer, 0.6 parts of foaming agent, 0.4 parts of foam regulator, 0.2 parts of catalyst, 0.5 parts of crosslinking agent , 0.3 parts of foam stabilizer, 25 parts of glyoxal, and 280 parts of water.
[0042] The particle size of the corn stalk powder is ≤300 μm, and the moisture content is ≤14%.
[0043] Th...
Embodiment 2
[0061]An environmentally friendly brick, comprising a hollow brick as a brick body shell and a new type of foam material filled in the cavity of the brick body, the hollow brick includes the following raw materials in parts by weight: 45 parts of cement, 35 parts of shale ore, powder 25 parts of coal ash, 8 parts of tailings sand, and 6 parts of kaolin; the new foaming material includes the following raw materials in parts by weight: 25 parts of cement, 2 parts of calcium silicate, 2 parts of calcium sulfate, and 2 parts of bentonite , 1 part of magnesium borate, 1.5 parts of corn straw powder, 0.6 parts of AR glass fiber, 0.4 parts of carbon fiber, 1.5 parts of water reducer, 0.2 parts of foaming agent, 0.2 parts of foam regulator, 0.1 part of catalyst, 0.3 parts of crosslinking agent , 0.1 parts of foam stabilizer, 20 parts of glyoxal, and 240 parts of water.
[0062] The particle size of the corn stalk powder is ≤300 μm, and the moisture content is ≤14%.
[0063] The water...
PUM
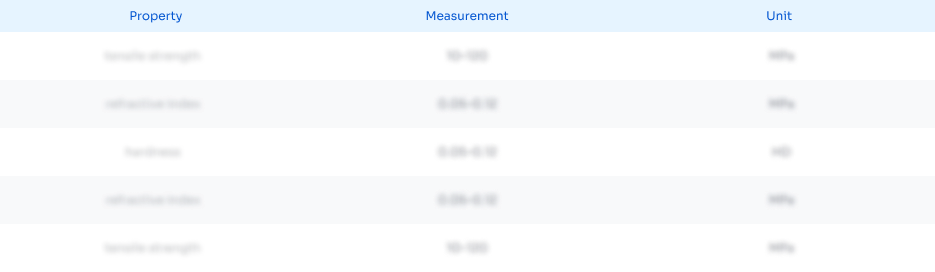
Abstract
Description
Claims
Application Information

- Generate Ideas
- Intellectual Property
- Life Sciences
- Materials
- Tech Scout
- Unparalleled Data Quality
- Higher Quality Content
- 60% Fewer Hallucinations
Browse by: Latest US Patents, China's latest patents, Technical Efficacy Thesaurus, Application Domain, Technology Topic, Popular Technical Reports.
© 2025 PatSnap. All rights reserved.Legal|Privacy policy|Modern Slavery Act Transparency Statement|Sitemap|About US| Contact US: help@patsnap.com