High-linearity quasi-zero stiffness vibration isolator
A technology with quasi-zero stiffness and high linearity, applied in the field of vibration isolation devices, can solve the problems of difficult control and complex dynamic behavior in the field of active control, and achieve the effects of high linearity, stable dynamic behavior and excellent vibration isolation performance
- Summary
- Abstract
- Description
- Claims
- Application Information
AI Technical Summary
Problems solved by technology
Method used
Image
Examples
Embodiment Construction
[0027] The present invention is described in more detail below in conjunction with accompanying drawing example:
[0028] combine Figure 1-11 , The high linearity quasi-zero stiffness vibration isolator of the present invention includes a support plate 1, an upper and lower frame, eight sets of horizontal spring mechanisms, eight sets of connecting rod mechanisms, a set of three permanent magnet mechanisms, four sets of vertical support mechanisms and a base 22. The support plate 1 is processed with installation through holes for supporting the vibration-isolated object, and is connected with the upper frame 14 by bolts. Eight sets of horizontal spring mechanisms are respectively installed on the cantilever beams protruding from the upper and lower frames. Four sets are respectively installed on the upper frame 14 and the lower frame 21. A linkage mechanism is designed between the horizontal spring mechanism and the three permanent magnet mechanisms, which are connected by pi...
PUM
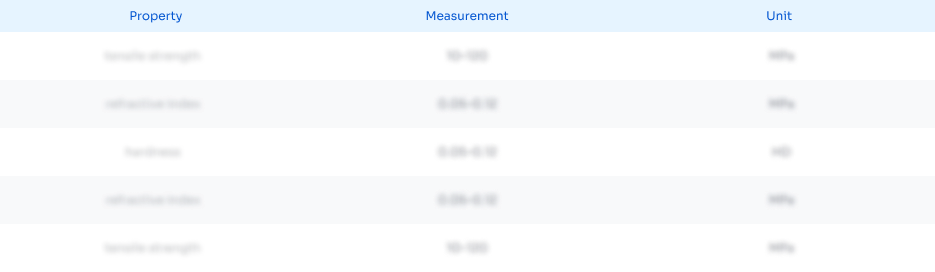
Abstract
Description
Claims
Application Information

- Generate Ideas
- Intellectual Property
- Life Sciences
- Materials
- Tech Scout
- Unparalleled Data Quality
- Higher Quality Content
- 60% Fewer Hallucinations
Browse by: Latest US Patents, China's latest patents, Technical Efficacy Thesaurus, Application Domain, Technology Topic, Popular Technical Reports.
© 2025 PatSnap. All rights reserved.Legal|Privacy policy|Modern Slavery Act Transparency Statement|Sitemap|About US| Contact US: help@patsnap.com