Method for thermoelectric dip plating of machine tool component
A technology for parts and machine tools, which is applied in the field of hot-dip plating of machine tool parts, can solve the problems of insufficient bonding, insufficient coating, and processing technology that cannot meet the needs of machine tools, so as to achieve good fluidity and avoid fragile layers.
- Summary
- Abstract
- Description
- Claims
- Application Information
AI Technical Summary
Problems solved by technology
Method used
Examples
specific Embodiment 1
[0012] A method for thermoelectric dip-plating of machine tool parts, the composition is taken by mass percentage: 65% zinc, 30% aluminum, 3% silicon, 2% nickel, and its specific dip-plating steps are:
[0013] (1) Rinse the machine tool parts with clean water for 3 times first, then soak them in boric acid for 5 minutes, rinse them with clean water once more, place them in a dryer for 30 minutes at 200°C, and then cool them down naturally;
[0014] (2) Put the machine tool parts processed in step (1) into a heating furnace for oxidative carbon removal at 400°C, then cool naturally, and then place them in a reduction furnace for residue removal at 800°C;
[0015] (3) Melt zinc, aluminum, silicon, and nickel into the plating pool in sequence. After 30 minutes of complete melting, immerse the machine tool parts treated in step (2) and protected by the reducing atmosphere into the plating pool, and turn on the power to carry out After 40 minutes of thermoelectric dipping, the mac...
specific Embodiment 2
[0016] A method for thermoelectric dip-plating of machine tool parts, the composition is taken by mass percentage: 70% zinc, 25% aluminum, 3% silicon, 2% nickel, and its specific dip-plating steps are:
[0017] (1) Rinse the machine tool parts with clean water for 5 times, then soak them in boric acid for 7 minutes, rinse them with clean water for 3 times, place them in a dryer at 240°C for 40 minutes, and then cool them down naturally;
[0018] (2) Put the machine tool parts processed in step (1) into a heating furnace for oxidative decarburization at 500°C, then cool naturally, and then place them in a reduction furnace at 900°C for residue removal;
[0019] (3) Melt zinc, aluminum, silicon, and nickel into the plating pool in sequence. After 40 minutes of complete melting, immerse the machine tool parts treated in step (2) and protected by the reducing atmosphere into the plating pool, and turn on the power to carry out After 50 minutes of thermoelectric dipping, the dip-co...
specific Embodiment 3
[0020] A method for thermoelectric dip-plating of machine tool parts, the composition is taken by mass percentage: 68% zinc, 28% aluminum, 3.8% silicon, 0.2% nickel, and its specific dip-plating steps are:
[0021] (1) Rinse the machine tool parts with clean water for 4 times, then soak them in boric acid for 6 minutes, rinse them with clean water for 2 times, place them in a dryer for 35 minutes at 220°C, and then cool them down naturally;
[0022] (2) Put the machine tool parts processed in step (1) into a heating furnace for oxidative decarburization at 450°C, then cool naturally, and then place them in a reduction furnace at 850°C for residue removal;
[0023] (3) Melt zinc, aluminum, silicon, and nickel into the plating pool in order. After 35 minutes of complete melting, immerse the machine tool parts treated in step (2) and protected by the reducing atmosphere into the plating pool, and turn on the power to carry out After 45 minutes of hot electric dipping, the machine...
PUM
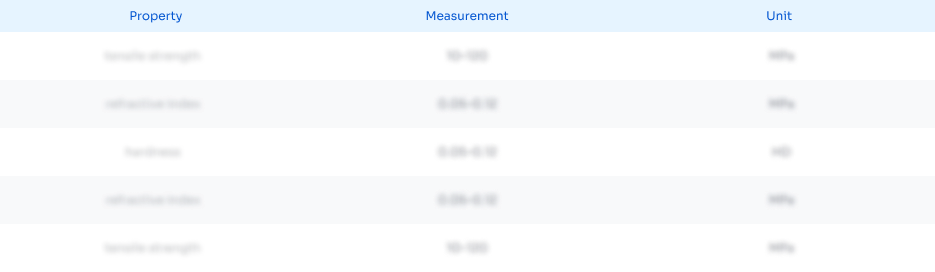
Abstract
Description
Claims
Application Information

- R&D Engineer
- R&D Manager
- IP Professional
- Industry Leading Data Capabilities
- Powerful AI technology
- Patent DNA Extraction
Browse by: Latest US Patents, China's latest patents, Technical Efficacy Thesaurus, Application Domain, Technology Topic, Popular Technical Reports.
© 2024 PatSnap. All rights reserved.Legal|Privacy policy|Modern Slavery Act Transparency Statement|Sitemap|About US| Contact US: help@patsnap.com