A comprehensive recovery and treatment process of electrolytic manganese anode slime
A technology of recycling and electrolytic manganese, which is applied in the field of metallurgy, can solve the problems of unreasonable utilization, complex composition and structure, and insufficient consideration of the connection in the field of electrolytic manganese, so as to achieve good industrial application prospects, simple and easy production and operation, and effective Conducive to the effect of organizing production
- Summary
- Abstract
- Description
- Claims
- Application Information
AI Technical Summary
Problems solved by technology
Method used
Image
Examples
Embodiment 1
[0036] A kind of embodiment of electrolytic manganese anode slime comprehensive recovery treatment process of the present invention, its process flow is as follows figure 1 shown, including the following steps:
[0037] (1) Add 5t of electrolytic manganese anode slime (see Table 1 for the composition of the anode slime) to a volume of 150m 3 in the leaching tank;
[0038] (2) Add electrolytic manganese anolyte 100m into the leaching tank 3 (the composition is shown in Table 2), and the stirring is started simultaneously;
[0039] (3) Pass into SO 2 Cylinder gas (SO 2 content>99.5%, gas density under standard conditions is 2.86g / L), for leaching reaction, SO 2 The access speed is 300m 3 / h, the reaction temperature is 85°C, and the reaction time is 3.13h;
[0040] (4) After the leaching reaction is completed, add flocculant to the leaching tank, separate by natural sedimentation, and the gained supernatant is a solution containing manganese sulfate (anolyte after leachin...
Embodiment 2
[0048] A kind of electrolytic manganese anode slime comprehensive recycling process of the present invention, its technological process is as follows figure 1 shown, including the following steps:
[0049] (1) Add 3t of electrolytic manganese anode slime (see Table 4 for the composition of the anode slime) to a volume of 150m 3 in the leaching tank;
[0050] (2) Add electrolytic manganese anolyte 100m into the leaching tank 3 (the composition is shown in Table 5), and the stirring is started simultaneously;
[0051] (3) Pass in the SO produced by burning sulfur 2 Gas (SO 2 content>17%, the gas density under standard conditions is 1.56g / L), for leaching reaction, SO 2 Access speed is 1000m 3 / h, the reaction temperature is 54°C, and the reaction time is 7h;
[0052] (4) After the leaching reaction is completed, add flocculant to the leaching tank, and through vacuum belt filtration, the resulting filtrate is a solution containing manganese sulfate (anolyte after leaching...
PUM
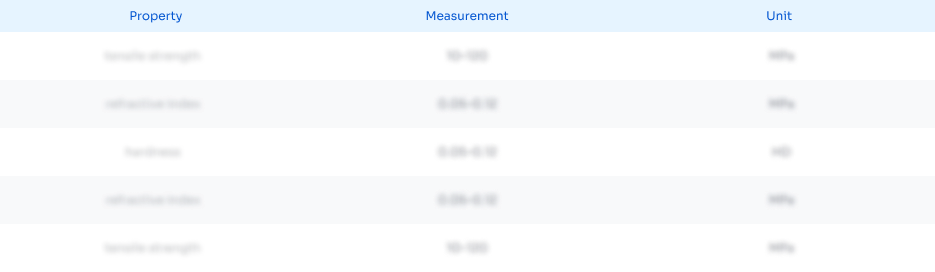
Abstract
Description
Claims
Application Information

- Generate Ideas
- Intellectual Property
- Life Sciences
- Materials
- Tech Scout
- Unparalleled Data Quality
- Higher Quality Content
- 60% Fewer Hallucinations
Browse by: Latest US Patents, China's latest patents, Technical Efficacy Thesaurus, Application Domain, Technology Topic, Popular Technical Reports.
© 2025 PatSnap. All rights reserved.Legal|Privacy policy|Modern Slavery Act Transparency Statement|Sitemap|About US| Contact US: help@patsnap.com