Heat treatment technology for reducing deformation of GCr15 thin-wall conical ring
A cone ring and thin-walled technology is applied in the field of reducing heat treatment deformation of GCr15 thin-walled cone rings, which can solve the problems of neglecting the deformation of GCr15 thin-walled parts, increasing machining costs, and large grinding allowance, so as to reduce deformation , The effect of reducing the cost of grinding and reducing the grinding allowance
- Summary
- Abstract
- Description
- Claims
- Application Information
AI Technical Summary
Problems solved by technology
Method used
Image
Examples
Embodiment
[0043]Taking the heat treatment process of a certain type of Φ136mm×19.5mm thin-walled cone ring as an example, the heat treatment technical requirements are: surface hardness 58-62HRC, ellipticity deformation ≤ 0.20mm (ellipticity deformation before heat treatment ≤ 0.10mm). A heat treatment process for reducing the deformation of the GCr15 thin-walled cone ring in this embodiment specifically includes the following steps:
[0044] (1) Parts preparation: The GCr15 billet after spheroidizing annealing is machined into a thin-walled cone ring part. Among them, the chemical composition of the GCr15 billet (GB / T18254-2002) is: C: 0.95~1.05; Mn: 0.20~ 0.40; Si: 0.15~0.35; S: ≤0.020; P: ≤0.027; Cr: 1.30~1.65; Mo: ≤0.10; Ni: ≤0.30; Cu: ≤0.25; Ni+Cu: ≤0.50; Spheroidizing annealing, after spheroidizing annealing, can make the subsequent quenching effect uniform, reduce quenching deformation, increase quenching hardness, improve the cutting performance of parts, and improve the wear re...
PUM
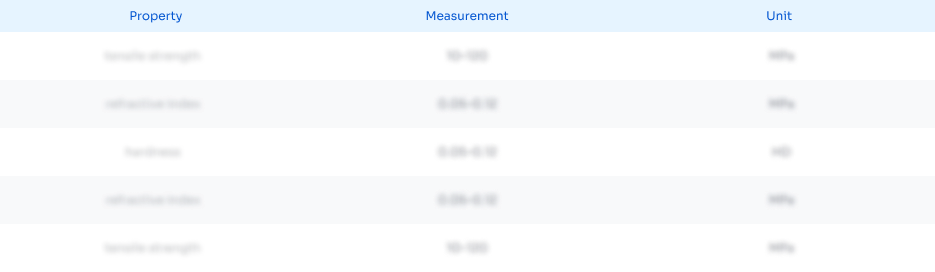
Abstract
Description
Claims
Application Information

- R&D
- Intellectual Property
- Life Sciences
- Materials
- Tech Scout
- Unparalleled Data Quality
- Higher Quality Content
- 60% Fewer Hallucinations
Browse by: Latest US Patents, China's latest patents, Technical Efficacy Thesaurus, Application Domain, Technology Topic, Popular Technical Reports.
© 2025 PatSnap. All rights reserved.Legal|Privacy policy|Modern Slavery Act Transparency Statement|Sitemap|About US| Contact US: help@patsnap.com