Intelligent and compact type welding line visual tracking system
A visual tracking and compact technology, applied in the field of visual tracking, can solve the problems of reducing equipment intelligence, occupying a large space, and processing result errors, etc., and achieving the effect of compact structure and easy installation or disassembly.
- Summary
- Abstract
- Description
- Claims
- Application Information
AI Technical Summary
Problems solved by technology
Method used
Image
Examples
Embodiment 1
[0040] This embodiment provides an intelligent and compact welding seam visual tracking system, which includes: a housing 1, an upper cover 2, an installation firmware 3, a camera 4, a laser 5, an optical path adjustment module 6, a driving device 7, and a control system 8.
[0041] like figure 1 As shown, it is a schematic diagram of the inner structure of the housing in Embodiment 1; as figure 2 Shown is a schematic diagram of the outer structure of the housing in Embodiment 1. The housing 1 includes a bottom plate 11 , a left side plate 12 , a right side plate 13 and a sloping plate 14 , and the above-mentioned bottom plate 11 , left side plate 12 , right side plate 13 and sloping plate 14 are integral structures. The bottom plate 11 is provided with a bottom plate through hole 115 and a first assembly hole 116, and the first assembly hole 116 is a through hole. The base plate 11 also has a base plate first slot 111 , a base plate second slot 112 , a base plate third sl...
Embodiment 2
[0061] The difference between this embodiment and Embodiment 1 is that the image sharpness comparison algorithm involved in the process of performing the best camera focal length adjustment is different. The image sharpness comparison algorithm in this embodiment includes time domain form and frequency domain form. form, the focal length of the fixed-focus lens 42 is adjusted based on the spectrum in its frequency domain form. The image sharpness comparison function is:
[0062] In the formula, Y is the comparison function value, X(a,b) is the brightness of the pixel in row a and column b, and X a (a, b), X b (a, b) represent the difference between the brightness of row a and column b and the brightness of adjacent pixels, X a (a,b)=X(a,b+1)-X(a,b),X b (a,b)=X(a+1,b)-X(a,b).
[0063] The above image sharpness comparison operation is performed in the time domain, and the algorithm in the frequency domain after conversion is:
[0064] S = ...
Embodiment 3
[0068] This embodiment implements the image sharpness comparison method involved in the process of adjusting the best focal length of the camera, and uses the combination of the comparison algorithm in Embodiment 1 and the image sharpness comparison algorithm in Embodiment 2 to enhance the determination of the best focal length. accuracy.
[0069]To sum up, the intelligent and compact welding seam visual tracking system provided by this embodiment can realize high-precision tracking of the welding seam.
PUM
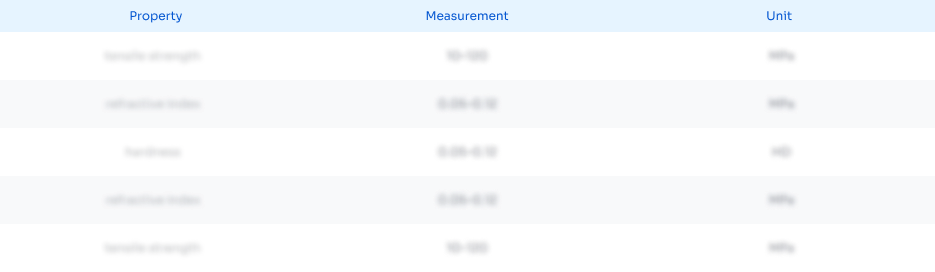
Abstract
Description
Claims
Application Information

- R&D
- Intellectual Property
- Life Sciences
- Materials
- Tech Scout
- Unparalleled Data Quality
- Higher Quality Content
- 60% Fewer Hallucinations
Browse by: Latest US Patents, China's latest patents, Technical Efficacy Thesaurus, Application Domain, Technology Topic, Popular Technical Reports.
© 2025 PatSnap. All rights reserved.Legal|Privacy policy|Modern Slavery Act Transparency Statement|Sitemap|About US| Contact US: help@patsnap.com